Summary:
What Are the Differences Between Hot and Cold Rolling? A Comprehensive Guide
Hot Rolling: Forging Strength in Heat
Cold Rolling: Precision in the Chill
Choosing the Right Technique: Factors to Consider
In the realm of metal manufacturing, the processes of hot and cold rolling stand as two fundamental techniques, each with its own unique set of characteristics and advantages. it’s crucial to delve into the intricacies of these methods to provide valuable insights for those seeking a deeper understanding of metal forming processes. In this blog post, we will explore the disparities between hot and cold rolling, shedding light on the key aspects that make each technique distinct.
Before we dive into the differences, let’s establish a foundation by briefly defining hot and cold rolling. Both are metal forming processes used to shape and deform metal sheets or bars, but they operate under different temperature conditions, resulting in distinct material properties.
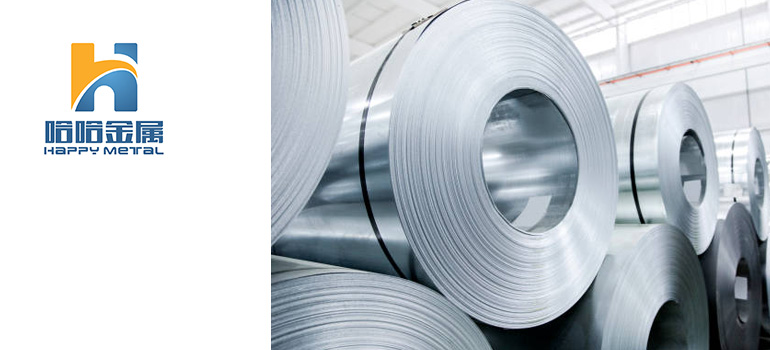
Hot Rolling: Forging Strength in Heat
Hot rolling involves processing metal at elevated temperatures, typically above the material’s recrystallization temperature. This method is renowned for its ability to shape large pieces of metal efficiently, offering numerous advantages in terms of reducing grain defects and enhancing mechanical properties. The increased temperature during hot rolling leads to a malleable material that is easier to deform, making it ideal for creating a wide range of products, from railroad tracks to structural beams.
Key Advantages of Hot Rolling:
Improved Ductility: The elevated temperatures reduce the material’s yield strength, making it more ductile and easier to deform.
Enhanced Mechanical Properties: Hot rolling refines the grain structure, resulting in improved mechanical properties such as toughness and strength.
Efficient Production: High temperatures enable faster processing and higher production rates, making hot rolling suitable for mass production.
Cold Rolling: Precision in the Chill
In contrast, cold rolling occurs at room temperature or slightly above it. This process imparts specific qualities to the metal, creating a smoother surface finish and tighter dimensional tolerances. Cold-rolled products find applications in industries that prioritize precision and surface quality, such as automotive, aerospace, and appliances.
Key Advantages of Cold Rolling:
Superior Surface Finish: Cold rolling produces a smoother surface, ideal for applications where aesthetics and surface quality are paramount.
Tighter Tolerances: The process allows for tighter dimensional control, resulting in more precise and consistent products.
Work-Hardening Effect: Cold rolling induces work hardening, improving the material’s hardness and strength.
Choosing the Right Technique: Factors to Consider
Deciding between hot and cold rolling depends on various factors, including the type of metal, required properties of the final product, and cost considerations. Manufacturers often weigh the trade-offs between efficiency and precision when selecting the most suitable method for their applications.
In the dynamic world of metal manufacturing, the choice between hot and cold rolling is a crucial decision that profoundly influences the characteristics of the final product. By understanding the differences between these two techniques, manufacturers can make informed choices that align with their specific needs and objectives. As we continue to advance in the field of metalworking, the synergy between hot and cold rolling remains integral to shaping the future of industrial production.