Summary:
Understanding Carbon Steel Pipe Thickness: A Comprehensive Overview
What is Carbon Steel Pipe Thickness
Factors Influencing Carbon Steel Pipe Thicknes
Measuring Carbon Steel Pipe Thickness Accuratel
Selecting the Right Carbon Steel Pipe Thickness for Different Applications
What is Carbon Steel Pipe Thickness?
Carbon steel pipe thickness refers to the measurement of the wall thickness of pipes made from carbon steel. This seemingly simple metric is crucial in determining how well a pipe can handle different types of stress and pressure during its service life. Let’s break this down further to understand why it’s so important.
Definition and Importance
At its core, the thickness of a carbon steel pipe is simply how thick the walls of the pipe are. This measurement is typically given in millimeters or inches and is a fundamental specification used to ensure that pipes meet the necessary strength and safety requirements for their intended use. The thickness plays a critical role in the pipe’s durability, strength, and resistance to various forms of stress, including internal pressure and external impacts. Thicker pipes generally offer better resistance to pressure and more extended service life, which is why selecting the correct thickness is vital for both safety and performance.
Industry Standards for Thickness
Industry standards provide guidelines on the acceptable range of pipe thicknesses for various applications. Standards like those from ASTM (American Society for Testing and Materials) and ISO (International Organization for Standardization) outline the minimum and maximum thicknesses required for different types of carbon steel pipes. These standards help ensure consistency and reliability across the industry, so that pipes perform as expected under the conditions they are designed for. Familiarity with these standards is essential for engineers and procurement professionals when specifying or purchasing carbon steel pipes.
How Thickness Affects Pipe Performance
The thickness of a carbon steel pipe directly impacts its performance. For instance, a thicker pipe wall enhances the pipe’s ability to withstand high pressure and harsh environmental conditions, making it suitable for applications like oil and gas pipelines or high-pressure steam systems. Conversely, thinner pipes might be adequate for less demanding applications where pressure and environmental factors are not as extreme. Additionally, the pipe’s weight and cost increase with thickness, which can influence project budgets and logistics. Therefore, balancing the required thickness with performance needs and cost considerations is a key aspect of pipe selection.
Factors Influencing Carbon Steel Pipe Thickness
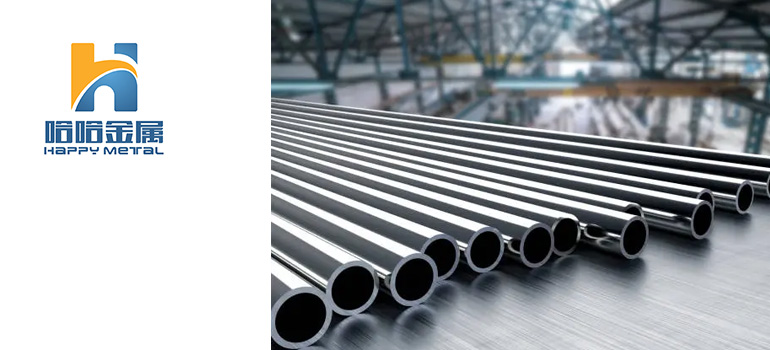
Choosing the appropriate thickness for carbon steel pipes involves several key factors, each of which can significantly affect the pipe’s performance, lifespan, and cost. Here’s a closer look at the primary factors influencing pipe thickness:
Material Strength and Pressure Ratings
The strength of the carbon steel material is a critical determinant of pipe thickness. The required thickness of a pipe is closely related to the pressure it must withstand. Higher pressure requirements generally necessitate thicker walls to ensure that the pipe can handle the stress without deforming or failing. For instance, pipelines used in the oil and gas industry often require thicker walls due to the high pressures involved in transporting these materials. Thus, selecting the appropriate pipe thickness involves matching the material strength to the specific pressure rating required for the application.
Environmental Conditions and Usage
Environmental factors play a significant role in determining the necessary thickness of carbon steel pipes. Pipes exposed to extreme weather conditions, corrosive substances, or high temperatures may require increased thickness to withstand these external influences. For example, pipes used in marine environments, where they are subject to saltwater corrosion, often need thicker walls to enhance their resistance to corrosion. Similarly, pipes designed for transporting high-temperature fluids might require additional thickness to cope with thermal expansion and other heat-related stresses. Understanding the specific environmental conditions and intended usage of the pipe is crucial for selecting the appropriate thickness.
Manufacturing and Quality Control
The manufacturing process and quality control standards also impact the thickness of carbon steel pipes. Variations in manufacturing techniques can lead to slight differences in pipe thickness within a given range. To ensure that pipes meet design specifications and industry standards, manufacturers must adhere to rigorous quality control procedures. These procedures include thickness measurement, material testing, and welding quality inspections to guarantee the final product’s accuracy and consistency. Therefore, being aware of the quality control requirements during the manufacturing process is essential for ensuring the precision of pipe thickness.
Measuring Carbon Steel Pipe Thickness Accurately
Accurate measurement of carbon steel pipe thickness is crucial for ensuring that pipes meet performance specifications and safety standards. Here’s how you can effectively measure thickness and handle common challenges:
Tools and Techniques for Measurement
To measure carbon steel pipe thickness accurately, various tools and techniques are employed. The most common tool is a micrometer, which provides precise measurements by directly measuring the pipe wall thickness at various points. Another widely used method is ultrasonic testing, which involves sending sound waves through the pipe and measuring the time it takes for the waves to return, thereby determining the thickness. Each method has its advantages: micrometers are ideal for quick checks, while ultrasonic testing is effective for assessing thicker pipes and those with protective coatings.
Common Measurement Challenges
Several challenges can arise when measuring pipe thickness. One challenge is the presence of coatings or corrosion, which can affect the accuracy of measurements. For instance, pipes with thick coatings might require the coating to be removed or adjusted for an accurate reading. Additionally, pipes with irregular surfaces or heavy corrosion can lead to inconsistent measurements. Ensuring that the measurement tool is properly calibrated and the pipe surface is prepared for accurate assessment can help mitigate these issues.
Best Practices for Accurate Results
To ensure the most accurate measurements, follow these best practices:
Calibrate Instruments Regularly: Ensure that measurement tools are regularly calibrated according to manufacturer guidelines to maintain accuracy.
Measure at Multiple Points: Take measurements at several locations around the pipe to account for potential irregularities and obtain a comprehensive understanding of the pipe’s thickness.
Prepare the Surface: Clean the pipe surface before measurement to remove any coatings, rust, or debris that could affect the reading.
Document Measurements: Record measurements systematically to track variations and ensure compliance with specifications.
Selecting the Right Carbon Steel Pipe Thickness for Different Applications
Choosing the appropriate thickness for carbon steel pipes is crucial for ensuring optimal performance and safety across various applications. Here’s a guide to help you select the right thickness for different scenarios:
Residential vs. Industrial Uses
For residential applications, such as water supply lines or heating systems, the required pipe thickness is generally lower because the pressures and stresses are relatively mild. Standard thicknesses that meet domestic requirements are usually sufficient. In contrast, industrial applications, like those in manufacturing plants or chemical processing facilities, often involve higher pressures and more severe conditions. These applications typically require thicker pipes to handle the increased stress and ensure longevity and reliability.
High Pressure vs. Low Pressure Applications
Pipes designed for high-pressure applications, such as those used in oil and gas pipelines or high-pressure steam systems, need to have greater wall thickness to safely contain the high internal pressures. The thickness helps prevent failures and maintains structural integrity. Conversely, pipes used in low-pressure applications, like drainage systems or low-pressure water lines, can be thinner since they are subject to less internal stress. It’s essential to match the pipe thickness to the specific pressure requirements to ensure safety and performance.
Cost Considerations and Trade-offs
Selecting a thicker pipe generally improves durability and safety but also increases the cost and weight of the pipe. Thicker pipes are more expensive and can lead to higher transportation and installation costs. Therefore, it’s important to balance the need for strength and durability with the budgetary constraints of your project. Consider the long-term benefits of thicker pipes, such as reduced maintenance and extended service life, when evaluating cost trade-offs.