Summary:
The Ultimate Guide to Seamless Stainless Steel Pipe: Everything You Need to Know
What is seamless stainless steel pipe
Manufacturing process of stainless steel pipes
Classification and specifications of stainless steel pipes
The advantages and applications of seamless stainless steel pipes
Manufacturing process of seamless stainless steel pipes
What is seamless stainless steel pipe?
A seamless stainless steel pipe is a type of tubing made from stainless steel without any welded joints during its production process. This seamless construction imparts excellent properties and diverse applications to the stainless steel pipe.
Compared to welded joints, seamless stainless steel pipes offer higher strength and corrosion resistance. Their seamless structure allows them to perform exceptionally well in high-temperature, high-pressure, and corrosive environments, making them suitable for various industrial sectors and applications such as petroleum, chemical, pharmaceutical, and food processing industries.
Seamless stainless steel pipes are typically manufactured from stainless steel billets using processes like hot rolling or cold drawing to ensure precise dimensional accuracy and surface quality. These pipes can be classified according to different standards and specifications to meet the requirements of various engineering projects and applications.
Manufacturing process of stainless steel pipes
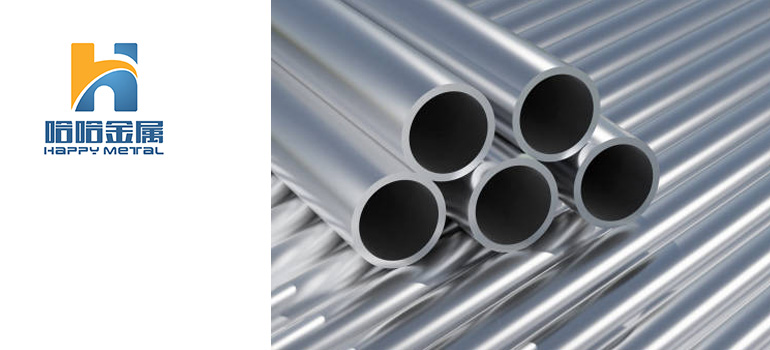
The manufacturing process of stainless steel pipes involves several steps to produce high-quality seamless tubes. Here’s an overview:
Material Selection: The process begins with selecting the appropriate grade of stainless steel based on the desired properties and application requirements.
Billet Production: Stainless steel billets are formed through casting or hot rolling. These billets serve as the raw material for manufacturing seamless pipes.
Heating: The billets are heated to the required temperature for hot working. This temperature is critical to ensure proper material flow and formability during subsequent processes.
Piercing: The heated billets are pierced to create a hollow shell. This process is typically done using a piercing mill or a rotary piercing machine, where a mandrel is used to initiate the hollow center.
Rolling: The pierced billet is then elongated and shaped into a seamless tube through a series of rolling processes. This can include hot rolling or cold rolling depending on the desired dimensions and mechanical properties of the final product.
Annealing: After forming, the seamless tube undergoes annealing, a heat treatment process that relieves internal stresses and improves the material’s ductility and toughness. Annealing also enhances the corrosion resistance of stainless steel.
Finishing: The seamless tube may undergo additional processes for finishing, such as straightening, polishing, or pickling, to achieve the desired surface finish and dimensional accuracy.
Testing and Inspection: Quality control measures are implemented throughout the manufacturing process to ensure that the seamless stainless steel pipes meet the specified standards and requirements. This may include non-destructive testing, dimensional inspection, and chemical analysis.
Cutting and Packaging: Once the seamless tubes pass inspection, they are cut to the desired lengths and packaged for shipping to customers or further processing.
By carefully controlling each step of the manufacturing process, stainless steel pipes with precise dimensions, excellent surface quality, and mechanical properties can be produced to meet the diverse needs of various industries.
Classification and specifications of stainless steel pipes
Stainless steel pipes are classified based on various criteria such as their manufacturing standards, grades, dimensions, and applications. Here’s an overview of the classification and specifications of stainless steel pipes:
Manufacturing Standards: Stainless steel pipes are manufactured according to various international standards, including:
– ASTM (American Society for Testing and Materials)
– AISI (American Iron and Steel Institute)
– JIS (Japanese Industrial Standards)
– DIN (Deutsches Institut für Normung)
– EN (European Norms)
– GB (Chinese National Standards)
Grades: Stainless steel pipes are available in different grades, each with its own unique properties and characteristics. Common grades include:
– 304/304L (Standard stainless steel grade, widely used for general-purpose applications)
– 316/316L (Marine-grade stainless steel with enhanced corrosion resistance)
– 321 (Stabilized stainless steel with improved high-temperature properties)
– 310/310S (High-temperature resistant stainless steel for furnace and heat exchanger applications)
– 2205 (Duplex stainless steel with high strength and corrosion resistance)
Dimensions: Stainless steel pipes come in various sizes and dimensions, including:
– Outer Diameter (OD): Ranging from small sizes (e.g., 1/8 inch) to large sizes (e.g., 48 inches or more)
– Wall Thickness: Varies depending on the application and pressure requirements
– Length: Standard lengths are typically 20 feet (6 meters), but custom lengths can also be produced
Types: Stainless steel pipes can be classified based on their manufacturing method and structure, including:
– Seamless Pipes: Produced without any welding seam, offering higher strength and corrosion resistance
– Welded Pipes: Manufactured by welding stainless steel plates or coils, available in various welding methods such as ERW (Electric Resistance Welding), SAW (Submerged Arc Welding), and TIG (Tungsten Inert Gas) welding
Applications: Stainless steel pipes are used in a wide range of applications across industries such as:
– Petrochemical and Chemical Processing
– Oil and Gas Exploration and Production
– Food and Beverage Processing
– Pharmaceutical and Biotechnology
– Construction and Architecture
– Automotive and Transportation
By understanding the classification and specifications of stainless steel pipes, manufacturers and end-users can select the appropriate material to meet their specific requirements and applications.
The advantages and applications of seamless stainless steel pipes
Seamless stainless steel pipes offer numerous advantages, making them widely used in various applications. Here are some key advantages and application areas:
Advantages:
Excellent Corrosion Resistance: Stainless steel inherently possesses excellent corrosion resistance, and the seamless design further enhances the pipe’s corrosion resistance, making it suitable for various corrosive environments.
High Strength and Pressure Resistance: Seamless stainless steel pipes, being formed from a single piece of steel without welded joints, exhibit higher strength and pressure resistance, suitable for high-pressure applications.
Superior High-Temperature Performance: Stainless steel maintains stable performance even at high temperatures, and the seamless design ensures excellent performance under high temperatures without deformation or annealing.
Smooth Interior and Exterior Surfaces: Seamless stainless steel pipes have smooth interior and exterior surfaces without pores or protrusions, facilitating fluid transportation and cleaning while reducing the likelihood of dirt and bacterial growth.
Good Machinability: Stainless steel is easy to machine and shape, catering to various complex shapes and size requirements.
Application Areas:
Oil and Gas Industry: Widely used in oil wells, pipeline transportation, refining, etc., due to their corrosion resistance and high-temperature properties.
Chemical Industry: Utilized in chemical plants’ piping systems, chemical reactors, etc., owing to their excellent corrosion resistance and pressure resistance.
Food Processing and Pharmaceuticals: Used for conveying food, pharmaceuticals, and bioproducts, requiring non-toxic, tasteless materials that are easy to clean.
Construction and Building Materials: Used in building structures for load-bearing and support, such as stair handrails, railings, etc., due to their aesthetic appeal and durability.
Aerospace: Employed in aerospace applications for manufacturing aircraft components, engine parts, etc., due to their lightweight, high strength, and high-temperature resistance.
Automotive Manufacturing: Used in automotive exhaust systems, chassis components, etc., requiring materials with high-temperature resistance and wear resistance.
In summary, seamless stainless steel pipes, with their excellent performance and diverse application areas, have become indispensable materials in many industrial and commercial fields.
Manufacturing process of seamless stainless steel pipes
The manufacturing process of seamless stainless steel pipe involves several crucial steps to ensure high-quality end products. Here’s an outline of the typical manufacturing process:
Material Selection: High-quality stainless steel is selected based on the desired properties and specifications of the final product. Factors such as corrosion resistance, mechanical strength, and temperature resistance are considered during material selection.
Billet Production: The selected stainless steel is initially cast into large billets through processes like continuous casting or hot rolling. These billets serve as the starting material for the seamless pipe manufacturing process.
Heating: The stainless steel billets are heated to a precise temperature range to make them more malleable and suitable for further processing. This heating process is crucial for ensuring uniform material properties throughout the billet.
Piercing: The heated billets are then pierced to form hollow shells using specialized piercing machines. This process involves pushing a mandrel through the center of the billet to create a hollow cavity.
Extrusion and Rolling: The pierced billets are further processed through extrusion or rolling processes to shape them into seamless tubes. During this stage, the billets are elongated and shaped into the desired dimensions while maintaining a seamless structure.
Heat Treatment: The seamless tubes undergo heat treatment processes such as annealing to improve their mechanical properties and remove internal stresses. Annealing also enhances the corrosion resistance and ductility of the stainless steel.
Finishing Operations: After heat treatment, the seamless tubes may undergo additional finishing operations such as straightening, cutting, and polishing to achieve the final dimensions and surface finish required for the intended application.
Testing and Inspection: Quality control checks are performed at various stages of the manufacturing process to ensure that the seamless stainless steel pipes meet the required specifications and standards. This includes dimensional checks, visual inspections, and non-destructive testing methods such as ultrasonic testing.
Packaging and Shipping: Once the seamless stainless steel pipes pass quality control checks, they are packed according to customer requirements and shipped to their destination for use in various industries and applications.
By following these steps meticulously, manufacturers can produce seamless stainless steel pipes with consistent quality and performance, meeting the demanding requirements of diverse industrial sectors.