Summary:
How to Maintain Stainless Steel Pipes: Best Practices for Durability and Efficiency
Understanding the Basics of Stainless Steel Pipe Maintenance
Routine Cleaning and Inspection for Stainless Steel Pipe Maintenance
Preventing Corrosion: Essential Tips for Stainless Steel Pipe Maintenance
Managing Pressure and Temperature Effects on Stainless Steel Pipes
Understanding the Basics of Stainless Steel Pipe Maintenance
Stainless steel pipes are widely used in various industries for their durability, resistance to corrosion, and ability to handle both high pressures and temperatures. However, like all industrial equipment, they require regular maintenance to ensure they continue to perform optimally. Proper stainless steel pipe maintenance not only extends the lifespan of the pipes but also ensures they operate efficiently, preventing unexpected breakdowns and costly repairs.
Importance of Regular Maintenance for Stainless Steel Pipes
You may think that stainless steel pipes, due to their robust nature, don’t require much attention. However, regular maintenance is essential to keep them functioning at their best. Without proper upkeep, issues such as blockages, corrosion, and leaks can develop over time, leading to decreased performance and potentially expensive repairs or replacements.
Regular maintenance helps in several ways:
- Preventing Costly Repairs: Catching issues early through routine checks can prevent them from becoming bigger problems down the road. Small cracks or signs of wear, if left unaddressed, can lead to pipe failure, resulting in costly downtime and repair bills.
- Extending Pipe Lifespan: Stainless steel pipes are designed to last, but that doesn’t mean they’re immune to wear and tear. A proactive maintenance approach ensures that your pipes serve you for many years without needing replacement.
- Ensuring Efficiency: A well-maintained pipe system runs more efficiently, improving the overall performance of the entire production or transport system. In applications where flow is critical, even a small issue like a clog can cause disruptions and slow down operations.
Regular maintenance schedules and checks should become a part of your overall operations. This not only saves you money in the long run but also minimizes unexpected downtime.
Common Issues in Stainless Steel Pipes and How to Prevent Them
While stainless steel pipes are known for their resilience, they are not completely immune to issues. Understanding these common problems is crucial to maintaining their performance. Here are some of the most frequent challenges you might encounter, along with solutions to prevent them:
- Corrosion: Even though stainless steel is resistant to corrosion, it’s not completely immune. In environments with high moisture, chloride exposure, or extreme temperatures, the surface of the pipe may still become susceptible to rust or pitting. Regular cleaning and inspection, combined with applying corrosion inhibitors or coatings, can prevent this issue.
- Buildup and Blockages: Over time, substances like grease, dirt, or scale can accumulate inside stainless steel pipes, restricting flow and causing blockages. Regular cleaning and descaling are important to prevent these buildups. Depending on the application, you may need to implement automated cleaning systems or schedule periodic maintenance to flush the pipes.
- Leaks and Cracks: Physical damage such as cracks or fractures can develop in stainless steel pipes, particularly at joints or welds. Inspecting pipes regularly for signs of wear, using high-quality welding techniques, and ensuring proper installation can prevent these issues.
Routine inspections and early intervention are key to catching these problems before they escalate.
Key Factors Affecting the Performance of Stainless Steel Pipes
Several factors can affect how well your stainless steel pipes perform, and understanding these factors is essential for effective stainless steel pipe maintenance.
- Environmental Factors: The environment in which the pipes are used plays a significant role in their longevity. For example, pipes used in coastal areas are more prone to corrosion due to the saltwater in the air. Similarly, pipes exposed to extreme temperatures (either very high or very low) may expand or contract, leading to stress and potential damage.
- Pipe Material and Grade: Stainless steel comes in various grades, and each has its own set of properties. For instance, 304 stainless steel is highly resistant to corrosion but may not be suitable for certain high-temperature or high-pressure environments, while 316 stainless steel is better for extreme conditions like marine environments.
- Flow Conditions: The flow inside the pipes—whether it’s liquids, gases, or solids—can affect pipe integrity. High-velocity flows can lead to erosion and wear, while stagnant areas may promote the growth of harmful bacteria or cause sediment buildup.
By understanding the basics of stainless steel pipe maintenance, you can ensure that your system runs efficiently and lasts longer. Regular inspections, cleaning, and attention to environmental factors are all key aspects of maintaining stainless steel pipes in top condition. Whether it’s preventing corrosion, reducing the risk of blockages, or ensuring the pipes can handle the demands of high-pressure or high-temperature environments, proactive maintenance is the best way to keep your pipes performing at their best.
Routine Cleaning and Inspection for Stainless Steel Pipe Maintenance
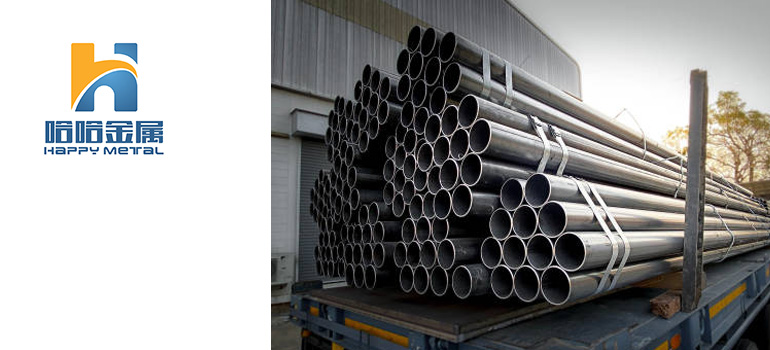
Routine cleaning and inspection are vital components of stainless steel pipe maintenance. Over time, pipes can accumulate debris, scale, or residue from the fluids they transport, which can impede flow, cause corrosion, or even lead to blockages. Regular cleaning and thorough inspections not only prevent these issues but also help identify early signs of wear or damage, ensuring that your system runs efficiently and extends the life of the pipes.
How to Properly Clean Stainless Steel Pipes
Cleaning stainless steel pipes is essential to maintain their functionality and appearance. Different systems may require different cleaning approaches depending on factors like the nature of the material being transported, the pipe’s location, and how often the system is used. Here’s a guide on how to clean stainless steel pipes properly:
Choose the Right Cleaning Methods: The cleaning method you choose should match the type of contamination you’re dealing with. For example:
- For light dirt and dust, water and mild detergents may be enough.
- For oil, grease, or sticky residues, more specialized cleaners like solvent-based degreasers or alkaline cleaners may be required.
- In cases where there is mineral buildup or scale, using descaling agents or a chemical cleaning process can be effective.
Mechanical Cleaning: For stubborn buildup, mechanical cleaning methods can be used. Brushes, scrapers, or sponge balls can be pushed through pipes to physically scrub away dirt and debris. In some cases, high-pressure water jetting is used to clean the interior of the pipes.
Automated Cleaning Systems: In larger or more complex systems, automated clean-in-place (CIP) systems are often installed. These systems allow pipes to be cleaned without being disassembled, reducing downtime and improving efficiency. CIP systems circulate cleaning agents through the pipes at high temperatures, ensuring thorough cleaning without manual intervention.
Avoid Harsh Chemicals: Stainless steel is resistant to corrosion, but some cleaning chemicals can damage its surface, leading to long-term issues. Always avoid chlorine-based cleaners or harsh acidic solutions unless they are specifically designed for stainless steel. Test any cleaning solution in a small, inconspicuous area before full use.
How to Inspect Stainless Steel Pipes for Signs of Wear
Inspection is equally important as cleaning when it comes to maintaining stainless steel pipes. Regular inspections help catch problems before they become critical, reducing the likelihood of unexpected failures. Here’s how to effectively inspect stainless steel pipes:
Visual Inspections: One of the simplest and most effective inspection methods is visual inspection. Check the external surfaces of the pipes for signs of:
- Corrosion or pitting (especially around welded joints or fittings).
- Cracks or deformities that could indicate a weakness in the material.
- Staining from moisture, oils, or chemicals that may have dripped onto the pipes.
- Regular visual inspections can help detect issues early before they compromise the integrity of the pipe.
Ultrasonic Testing: For a more thorough check, ultrasonic testing is a non-destructive method used to detect internal flaws such as cracks, thinning, or corrosion. Ultrasonic waves are sent through the pipe wall, and any changes in the wave’s frequency can indicate issues within the material. This is particularly useful in high-pressure or high-temperature applications where internal damage may not be visible from the outside.
Pressure Testing: Pressure testing is another essential part of pipe inspections, particularly in systems where the pipes carry fluids under high pressure. This test ensures that the pipes can withstand the operational pressures without leaks or failures. Common methods include hydrostatic pressure testing, where the pipes are filled with water and subjected to pressure higher than normal operating levels to check for leaks or weakness.
Thermal Imaging: Thermal imaging cameras can detect temperature variations along the pipe, which may indicate leaks, poor insulation, or internal blockages. This method is especially useful in identifying hidden problems without needing to disassemble the pipe system.
Thickness Measurement: Over time, stainless steel pipes can lose thickness due to corrosion, erosion, or wear. Measuring the pipe’s wall thickness periodically can help identify areas that have thinned to the point of requiring repair or replacement. Specialized tools like digital calipers or eddy current devices can be used for these measurements.
Maintaining the Internal Surface of Stainless Steel Pipes
While exterior cleaning and inspection are essential, maintaining the internal surface of stainless steel pipes is equally important for ensuring smooth, uninterrupted flow and avoiding corrosion or buildup that could affect performance.
- Descaling and Chemical Cleaning: Over time, mineral deposits, scale, and other substances can accumulate inside the pipes, especially in systems carrying water, steam, or fluids with high mineral content. Using a descaling solution can help break down these deposits, restoring smooth flow. Chemical cleaning should be done periodically, depending on the type of materials the pipes are carrying.
- Use of Pigging Systems: In some systems, particularly those used in the food, beverage, and pharmaceutical industries, pigging systems are employed to remove debris, sludge, or product residues from the interior of pipes. These automated systems use a soft foam “pig” that is pushed through the pipes, cleaning the interior without disassembling the system.
- Regular Flushing: For pipelines carrying corrosive fluids or chemicals, regular flushing is an essential maintenance practice. This helps prevent the buildup of contaminants and ensures that the fluid flow remains consistent. For systems with more aggressive fluids, such as wastewater treatment, regular flushing with water or cleaning solutions can keep internal surfaces free from corrosion-inducing materials.
- Preventing Bacterial Growth: In some applications, particularly food-grade or pharmaceutical piping, bacterial growth inside the pipes is a concern. Regular sanitization, use of biocides, and proper drainage of the pipes when not in use can help prevent microbial contamination.
Routine cleaning and inspection are essential for keeping your stainless steel pipes in optimal condition and preventing major issues that could disrupt operations. By selecting the right cleaning methods, performing regular visual and non-destructive inspections, and maintaining the internal surfaces, you can ensure that your pipes last longer, function more efficiently, and avoid costly repairs. Regular attention to these areas will pay off by extending the lifespan of the system, improving safety, and enhancing overall performance.
Preventing Corrosion: Essential Tips for Stainless Steel Pipe Maintenance
Corrosion is one of the most common issues that affect stainless steel pipes, despite their inherent resistance to rust and decay. When not properly maintained, even stainless steel can suffer from pitting, crevice corrosion, and other forms of degradation. Preventing corrosion is essential not only to extend the life of your pipes but also to ensure the continued efficiency and safety of your system. Below are some essential tips to help you protect your stainless steel pipes from corrosion.
Why Stainless Steel Pipes Corrode and How to Stop It
Though stainless steel is highly resistant to corrosion, certain factors can compromise its protective layer, leading to corrosion. Here’s why corrosion can still occur and how to mitigate it:
- Chlorides and Moisture: Stainless steel is particularly vulnerable to corrosion when exposed to chlorides (e.g., from saltwater or chlorinated cleaning agents) and moisture. These elements can break down the protective oxide layer that gives stainless steel its corrosion-resistant properties, leading to pitting or stress corrosion cracking.
Solution: To prevent chloride-induced corrosion, use marine-grade stainless steel (like 316-grade) for pipes exposed to saltwater or humid environments. Regularly clean the pipes to remove chloride residues and minimize their exposure. For areas prone to moisture, consider using corrosion-resistant coatings or wraps to shield the pipes.
- High Temperatures: High temperatures can accelerate corrosion, especially when combined with aggressive chemicals or steam. When exposed to heat, the protective chromium oxide layer may break down more quickly, making the stainless steel susceptible to damage.
Solution: For high-temperature applications, use alloys designed for heat resistance, such as 904L stainless steel. Keep pipes clean and well-maintained to prevent the build-up of contaminants that can increase the effects of heat.
- Lack of Oxygen: Stainless steel relies on oxygen to form the oxide layer that prevents corrosion. In environments where oxygen is scarce, such as in crevices or under deposits, corrosion is more likely to occur.
Solution: Regularly inspect areas where oxygen flow may be restricted, such as pipe joints or welds. Ensure that these areas are kept clean and free of debris. In confined spaces, consider using electrochemical protection methods like cathodic protection.
Choosing the Right Protective Coatings for Stainless Steel Pipes
While stainless steel naturally resists corrosion, applying protective coatings can provide an additional layer of defense, especially in high-risk environments. Here’s how to choose and apply the right coatings for your pipes:
Types of Coatings: There are several types of protective coatings available, each suited to different environments. Common options include:
- Epoxy Coatings: These coatings are effective for preventing moisture and chemical attacks. Epoxy coatings are commonly used in industries like water treatment and chemical processing.
- Polyurethane Coatings: Polyurethane provides good abrasion resistance and can protect pipes from both physical and chemical damage. It’s often used in environments with moderate to high traffic.
- Corrosion-Resistant Paints: Specially formulated paints, such as fluoropolymer coatings, can offer excellent resistance to both heat and corrosion, making them ideal for harsh industrial environments.
Solution: When selecting a coating, consider the specific operating conditions of your pipes, including temperature, exposure to chemicals, and environmental factors like humidity or saltwater. Consult with experts to choose the right coating material for your application.
Coating Application: Ensure that coatings are applied correctly to provide maximum protection. Surface preparation is critical for adhesion, so cleaning the pipes thoroughly before applying any coating is essential. If using a spray-on method, apply the coating evenly and ensure it covers all surfaces, including hard-to-reach areas.
Corrosion Resistance Based on Pipe Environment
The environment where your stainless steel pipes are installed significantly impacts their corrosion resistance. Factors such as temperature, humidity, chemical exposure, and mechanical stress should all be considered when implementing a corrosion prevention strategy.
- Marine and Coastal Environments: Pipes used in marine applications or coastal areas face the threat of saltwater exposure, which can cause rapid corrosion. Saltwater accelerates the breakdown of the protective oxide layer, leading to pitting corrosion.
- Chemical Processing Plants: In environments where pipes transport aggressive chemicals, the risk of corrosion from exposure to acids, alkalis, or other chemicals is heightened. Over time, these chemicals can degrade the stainless steel surface, leading to structural damage and leaks.
- Food and Beverage Industries: In the food and beverage industry, pipes are exposed to water, steam, cleaning agents, and food acids. Corrosion can occur if cleaning protocols are not followed or if bacteria are allowed to grow inside the pipes, leading to contamination risks.
Preventing corrosion is one of the most critical aspects of stainless steel pipe maintenance. By understanding the factors that contribute to corrosion and taking the necessary steps to protect your pipes, you can significantly extend their lifespan and ensure optimal performance. Regular cleaning, selecting the right materials, applying protective coatings, and understanding environmental impacts are all essential to combating corrosion. Proactive measures like these can help you avoid costly repairs, improve system efficiency, and maintain the integrity of your stainless steel pipes.
Managing Pressure and Temperature Effects on Stainless Steel Pipes
Stainless steel pipes are designed to handle a wide range of applications, including those that involve extreme pressure and temperature fluctuations. However, pressure and temperature can have significant effects on the performance and integrity of stainless steel pipes over time. Managing these factors properly is critical for ensuring the longevity, safety, and efficiency of your piping systems. Below, we’ll explore how pressure and temperature affect stainless steel pipes and provide strategies to mitigate these effects through proper maintenance and system design.
How Pressure Impacts Stainless Steel Pipe Performance
Pressure is one of the most important factors that influence the design, material choice, and maintenance needs of stainless steel pipes. The performance of a pipe under pressure depends not only on the internal fluid or gas being transported but also on the pipe’s ability to withstand the forces exerted on it.
- Pressure Limits and Pipe Strength: Every stainless steel pipe has a pressure rating, which indicates the maximum internal pressure the pipe can safely withstand without risk of rupture or deformation. If the pressure exceeds this limit, the pipe can become deformed, crack, or even burst, leading to dangerous situations and costly repairs.
Solution: Always ensure that the selected stainless steel pipe is rated for the intended pressure conditions. For high-pressure applications, consider using thicker pipes or pipes made from alloys with higher tensile strength, such as duplex stainless steel (like 2205), which offers superior resistance to both pressure and corrosion.
- Pressure Fluctuations: Sudden changes in pressure, known as pressure shocks or water hammer, can also damage stainless steel pipes. These pressure surges often occur when a valve is quickly opened or closed, causing a rapid change in the velocity of the fluid inside the pipe.
Solution: Install pressure relief valves and cushioning devices (such as air chambers or surge tanks) to absorb sudden pressure changes and prevent damage to the pipes. Additionally, consider using flexible pipe joints that can absorb shock and reduce stress on the pipe system.
- Fatigue and Stress Corrosion: Repeated pressure fluctuations over time can cause metal fatigue, leading to cracks or fissures. Stainless steel pipes that experience high, constant pressure are also at risk of stress corrosion cracking (SCC), which occurs when tensile stress and a corrosive environment interact.
Solution: To mitigate fatigue and SCC, conduct regular pressure testing to ensure that pipes remain within their pressure ratings. If your system is prone to frequent pressure variations, consider using expanded graphite gaskets or sealants to reduce stress concentration at pipe joints.
The Role of Temperature in Stainless Steel Pipe Integrity
Temperature plays a crucial role in the performance of stainless steel pipes. Extreme temperatures, whether high or low, can affect the material’s strength, corrosion resistance, and overall lifespan. Managing temperature effects is essential for maintaining the structural integrity and functionality of your pipes.
- Thermal Expansion and Contraction: Stainless steel, like all metals, expands when heated and contracts when cooled. This thermal expansion can lead to problems such as misalignment, increased stress on joints, and even pipe rupture if not properly managed.
- High-Temperature Effects: When exposed to high temperatures, stainless steel can lose its tensile strength and may become more susceptible to damage or failure. This is particularly important in applications like boilers, furnaces, or chemical reactors where temperatures can exceed 300°C (572°F).
- Low-Temperature Effects: On the other hand, extremely low temperatures can cause stainless steel to become brittle, especially in cryogenic applications or systems that transport liquefied gases like nitrogen or oxygen. At very low temperatures, the risk of cracking or fracture increases.
Managing the effects of pressure and temperature on stainless steel pipes is essential for ensuring long-term performance, safety, and reliability. By selecting the right materials, monitoring operating conditions, and implementing preventive measures like expansion joints, insulation, and pressure relief valves, you can minimize the risks associated with high-pressure and high-temperature environments. Regular inspections and maintenance are key to detecting potential issues early, so you can take action before they lead to system failures or costly repairs.