Summary:
Everything You Need to Know About Zinc Aluminum Magnesium Steel
What is Zinc Aluminum Magnesium Steel?
The History of Zinc Aluminum Magnesium Steel?
Zinc Aluminum Magnesium Steel advantages?
Use cases of Zinc Aluminum Magnesium Steel
Zinc Aluminum Magnesium steel is a new type of metal coating product that’s been used primarily by many of China’s steel mills. However, before you decide on whether this should be your new coating product of choice. You need to first understand what it is, its history, and its advantages over other coating products. Without further ado, let’s get started.
What Is Zinc Aluminum Magnesium Steel?
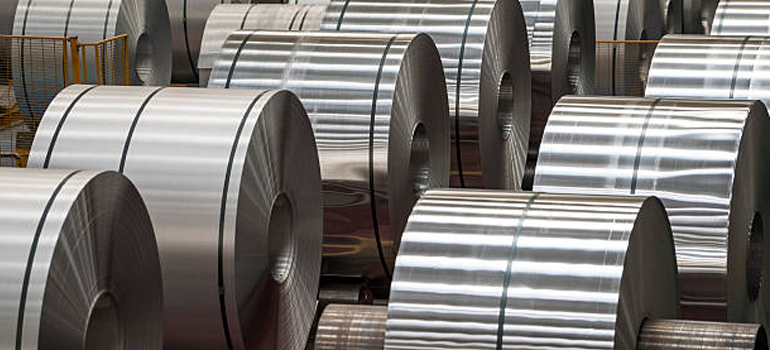
For those of you that are unfamiliar, Zinc Aluminum Magnesium coating, as defined by the European Standard EN10346-2015, is a ternary alloy coating with zinc as its primary component and aluminum and magnesium contents ranging from 1.5 to 8% (where the magnesium level is not less than 0.2%).
There was a lot of complicated jargon mentioned in that definition. To make it easier for the average reader, below is a breakdown of what was said:
- Zinc, Aluminum, and Magnesium are types of metal that are in this case being used to create Zinc Aluminum Magnesium Steel.
- The European Standard EN10346-2015 is a standard used for hot-dip coated products such as low carbon steels for cold forming, steels for construction, etc. In this case, we are using it as a standard for Zn-Al-Mg Steel.
- A ternary alloy refers to three elements combined where the result has different metallic characteristics from the original three elements.
The History of Zinc Aluminum Magnesium Steel
According to the industry, it’s been agreed upon that Nisshin Steel and Nippon steel – two Japanese steel mills, produced and promoted zinc, aluminum, and magnesium coated steel for the first time on a commercial scale.
However, American steel producers had begun researching and manufacturing zinc, aluminum, and magnesium coating as early as the 1960s and 1970s. But the difference is that they did not promote it on a commercial scale like Nisshin Steel and Nippon Steel did.
Nisshin Steel and Nippon Steel made significant improvements and started mass-producing zinc, aluminum, and magnesium alloy coated steel sheets in the 1990s after intense research and development work on coated steels with these elements..
Subsequently, significant steel corporations including ArcelorMittal, Thyssenkrupp Steel, Tata Steel Europe, and Australian steel giant BlueScope also created comparable products under their own trademarks.
In recent years, major corporations have started to produce Zn-Al-Mg coated steel as well as Chinese steel mills which followed suit.
Zinc Aluminum Magnesium Steel Advantages
Below is a list of Zinc Aluminum Magnesium Steel’s advantages over other popular and more common metal coatings. Use this list as a baseline for your understanding of whether you should switch to Zn- Al- Mg Steel.
Difficult to Peel Off
Because the steel sheet is coated with zinc, aluminum, and magnesium alloy and since it is thin and dense. This creates a coating that is very hard to peel off.
Excellent Corrosion Resistance
In some corrosive conditions, Zinc Aluminum Magnesium Steel has surprisingly strong corrosion resistance which makes it great for coastal areas and animal husbandry. Simonkolleite (Zn 5 (OH) 8 Cl 2 H 2 O), which creates and maintains a film-like coating on the surface of the coating and exerts excellent corrosion resistance, is formed when magnesium (Mg) is present in the coating. This is advantageous because it helps to promote the formation of a fine protective film that is very stable and well-structured. Galvanized steel’s corrosion resistance is 5–12 times lower than that of magnesium and Galvalume steel.
Great Alternative Coating
Zinc Aluminum Magnesium Steel can be a great alternative in place of some less demanding stainless steel or application scenarios like processing followed by galvanizing, which can make the user’s processing processes simpler.
Good Welding Performance
Magnesium can be used to a laser welding process to increase welding performance and decrease spatter of the weld accessories.
Good Alkali Resistance
Alkali resistance is likewise quite good, in addition. In comparison to hot-dip galvanized steel and hot-dip galvanized 5% aluminum alloy steel, this Zn- Al- Mg steels coil may achieve the same corrosion resistance while using fewer plating layers. Additionally, it can be used in place of stainless steel or aluminum plate due to its great resistance to red rust.
Excellent Coating Performance
Using Zinc-Aluminum-Magnesium as the metal coating is an excellent choice if you are looking for coating performance that is almost identical to pure zinc. It is a raw material for color coating and can be electrophoresed, post-sprayed, and employed in that way. And as an added benefit, It can greatly increase the corrosion resistance of the coated product due to its superior corrosion resistance beneath the layer.
Use Cases of Zinc Aluminum Magnesium Steel
Zinc Aluminum Magnesium Alloy Coated Sheet is frequently used in the metal forming industries of construction, road protection, three-dimensional parking lots, storage equipment, and automobile electromechanical devices.
All types of steel components, corrosion-resistant parts, keel ceilings, perforated plates, and cable trays may be produced using it. By switching to zinc aluminum magnesium coil, post-galvanizing and post-painting processes that are required for some applications can be skipped, lowering costs and shortening lead times.
The Zn -Al-Mg Coated Coil’s and its color steel’s corrosion resistance is five times greater than that of conventional Galvalume Steel, which addresses the issue of color steel’s rapid rusting in coastal areas as well as its short service life in applications such as structure engineering, power engineering, purification engineering, photovoltaic design, etc.
Products made of steel that has been coated with zinc, aluminum, and magnesium are widely used, particularly in civil construction such as keel ceilings, perforated plates, and cable bridges, especially in the agricultural sector in infrastructures such as breeding greenhouses, steel structures, steel components, greenhouses, breeding equipment, railways, roads, and many more.