Summary:
Carbon Steel Pipe Sizes Explained: A Beginner’s Guide
Introduction to Carbon Steel Pipe Sizes
Understanding Standard Carbon Steel Pipe Sizes
Factors Affecting the Selection of Carbon Steel Pipe Sizes
How to Measure and Calculate Carbon Steel Pipe Sizes
Introduction to Carbon Steel Pipe Sizes
In the world of construction and industrial applications, carbon steel pipes play a crucial role. They are used in a wide range of systems, from oil and gas pipelines to water treatment facilities. The size of these pipes significantly impacts both the performance and safety of the system. To fully grasp the importance of carbon steel pipe sizes, let’s start by understanding some basic concepts.
What Are Carbon Steel Pipes?
Carbon steel pipes are made from carbon steel, which is known for its high strength and durability. Carbon steel consists primarily of iron and carbon, with the carbon content determining the steel’s hardness and strength. These pipes are commonly used in environments that require the handling of high pressures and heavy loads, such as in industrial pipelines and structural supports. Their advantages include cost-effectiveness and a relatively straightforward manufacturing process.
Importance of Pipe Size in Construction and Industry
The size of a pipe is critical to the success of any engineering project. Choosing the correct pipe size affects not just the efficiency of fluid flow but also the overall safety of the system. A pipe that is too small might lead to excessive fluid velocity, increasing wear and the risk of failure. Conversely, a pipe that is too large could waste material and space, driving up costs. Therefore, understanding and selecting the appropriate carbon steel pipe size is essential to ensure the reliable operation of the system.
Overview of Different Carbon Steel Pipe Sizes
Carbon steel pipes come in various sizes, typically defined by two key specifications: outer diameter (OD) and wall thickness (WT). The outer diameter is the overall diameter of the pipe, while wall thickness refers to the thickness of the pipe walls. These dimensions determine the pipe’s pressure-bearing capacity and fluid-carrying ability. Common sizing standards include Nominal Pipe Size (NPS) and Diameter Nominal (DN), which may vary by region and application. Familiarizing yourself with these sizing standards will help you select the most appropriate carbon steel pipe for your specific needs.
In summary, understanding carbon steel pipe sizes and their related concepts is the first step in choosing the right piping material. By mastering these basics, you’ll be better equipped to plan and execute your engineering projects, ensuring that your piping systems operate safely and efficiently.
Understanding Standard Carbon Steel Pipe Sizes
When working with carbon steel pipes, it’s essential to grasp the standard sizing conventions that dictate their dimensions. Understanding these standards ensures that you select the right pipes for your project and adhere to industry requirements. Let’s break down the key aspects of standard carbon steel pipe sizes to help you make informed decisions.
Commonly Used Sizes and Their Applications
Carbon steel pipes come in a range of sizes, each suited to different applications. Some of the most common sizes include:
1/2 inch to 24 inches NPS: These sizes cover a broad spectrum of uses, from small residential water lines to large industrial pipelines. For instance, smaller sizes like 1/2 inch are typically used for household plumbing, while larger sizes such as 24 inches are used in major industrial processes, including oil and gas transport.
Sizes Over 24 inches NPS: For applications requiring even larger pipes, such as in heavy industrial or infrastructure projects, sizes can exceed 24 inches. These pipes are used in large-scale water supply systems, petrochemical industries, and other high-capacity systems.
Each size is designed to handle specific pressure levels and flow rates, so choosing the appropriate size is crucial for system performance and safety.
How to Read Carbon Steel Pipe Size Specifications
Understanding how to interpret pipe size specifications is vital for selecting the right product. Here are the main components you’ll encounter:
Nominal Pipe Size (NPS): This is a standardized designation used in North America. It refers to the approximate inside diameter of the pipe. For example, a pipe with an NPS of 6 inches generally has an actual inside diameter of approximately 6 inches, though this can vary slightly depending on the pipe schedule.
Pipe Schedule: This term refers to the thickness of the pipe walls. Common schedules include 40, 80, and 160, with higher numbers indicating thicker walls. The schedule impacts the pipe’s strength and pressure rating. For example, a Schedule 80 pipe is thicker and can handle higher pressures compared to a Schedule 40 pipe of the same nominal size.
Diameter Nominal (DN): Used primarily in international standards, DN is a designation that refers to the pipe’s approximate internal diameter in millimeters. For example, DN100 corresponds to a pipe with an internal diameter of approximately 100 mm.
By understanding these specifications, you can accurately select pipes that meet your project’s requirements.
Differences Between Nominal and Actual Pipe Sizes
It’s important to distinguish between nominal sizes and actual dimensions:
Nominal Size: This is a standardized label that provides a general idea of the pipe’s size. It simplifies the selection process but doesn’t always match the actual dimensions precisely.
Actual Dimensions: The actual dimensions of a pipe include its outer diameter and wall thickness. These measurements can vary slightly from the nominal size due to manufacturing tolerances and the pipe’s schedule. For precise applications, it’s crucial to consider these actual dimensions.
In summary, understanding standard carbon steel pipe sizes involves familiarizing yourself with commonly used sizes, how to read specifications, and the differences between nominal and actual dimensions. This knowledge will enable you to make well-informed decisions and ensure that your piping systems function effectively.
Factors Affecting the Selection of Carbon Steel Pipe Sizes
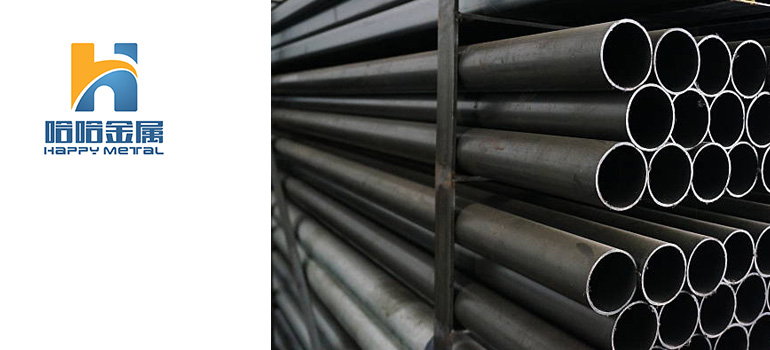
Choosing the right size for carbon steel pipes is a critical decision that can impact the efficiency, safety, and cost of your project. Several factors should be considered to ensure you select the most appropriate pipe size for your specific needs. Let’s explore these factors in detail:
Load and Pressure Requirements
One of the primary factors influencing pipe size is the load and pressure the pipe needs to handle:
Pressure Ratings: Carbon steel pipes are designed to withstand different pressure levels. The pipe size must be chosen based on the pressure requirements of the system. Larger pipes with thicker walls can handle higher pressures, while smaller or thinner pipes are suited for lower pressures. Understanding the maximum operating pressure of your system will guide you in selecting a pipe that ensures safety and durability.
Load Conditions: For applications involving heavy loads or structural support, such as in construction or industrial settings, the pipe size must accommodate these loads. Larger pipes with higher wall thicknesses provide greater strength and stability, reducing the risk of deformation or failure under load.
Environmental and Corrosion Considerations
The environmental conditions where the pipes will be installed play a crucial role in determining the appropriate size:
Corrosive Environments: If the pipes are exposed to corrosive substances or harsh environmental conditions, selecting a pipe with a larger diameter or thicker walls can provide added protection. Corrosion-resistant coatings or alloyed carbon steels might also be considered to enhance longevity.
Temperature Extremes: Pipes subjected to extreme temperatures may require special considerations. For instance, high temperatures can affect the strength and flexibility of the pipe material, while extremely low temperatures might increase the risk of brittleness. Ensure that the pipe size and material are compatible with the operating temperature range.
Compatibility with Other Components
Ensuring that the carbon steel pipe is compatible with other components in the system is essential for seamless integration:
Fittings and Connections: The pipe size must match the dimensions of fittings, valves, and other connection points within the system. Incompatibility can lead to leaks, operational inefficiencies, and additional costs for modifications.
System Design: The overall design of the system, including flow rates and pressure drops, must be taken into account. Proper sizing ensures that the pipe integrates well with the rest of the system and operates efficiently without causing unnecessary pressure losses or bottlenecks.
Future Expansion and Maintenance
Consideration for future changes to the system is also important:
Future Expansion: If there is a possibility of expanding the system or increasing flow rates in the future, it might be wise to select a slightly larger pipe size to accommodate these changes. This foresight can save time and costs associated with future upgrades.
Maintenance and Accessibility: Larger pipes might be more challenging to install and maintain, especially in confined spaces. Evaluate the ease of access and maintenance requirements to ensure that the pipe size aligns with practical considerations for system upkeep.
In summary, selecting the right carbon steel pipe size involves evaluating load and pressure requirements, environmental conditions, compatibility with other components, and considerations for future expansion and maintenance. By thoroughly assessing these factors, you can ensure that your piping system operates efficiently, safely, and cost-effectively.
How to Measure and Calculate Carbon Steel Pipe Sizes
Accurate measurement and calculation of carbon steel pipe sizes are crucial for ensuring that pipes fit correctly and function efficiently within a system. Here’s a step-by-step guide to measuring and calculating carbon steel pipe sizes to help you achieve precise results.
Tools and Methods for Accurate Measurement
To measure carbon steel pipes accurately, you’ll need the right tools and techniques:
Calipers: Use calipers to measure the outer diameter (OD) and wall thickness (WT) of the pipe. Digital calipers can provide precise measurements and are easier to read than manual ones.
Tape Measure: For larger pipes, a tape measure can be useful to measure the overall length and circumference. This tool is especially helpful for measuring pipes with larger diameters where calipers might be impractical.
Micrometers: For more precise measurements of wall thickness, especially on smaller pipes, micrometers are ideal. They can measure very thin dimensions accurately.
Pipe Sizers and Gauges: Specially designed pipe sizers and gauges can help you quickly identify standard pipe sizes and verify dimensions against industry standards.
Calculating Pipe Sizes Based on Flow Requirements
To ensure that a pipe can handle the required flow rate, you need to perform some calculations:
Determine Flow Rate: Start by calculating the flow rate required for your system, typically expressed in gallons per minute (GPM) or cubic meters per second (CMS). This is often determined by the specific needs of your application or system design.
Calculate Pipe Diameter: Use hydraulic calculations to determine the appropriate pipe diameter. For laminar flow conditions, you can use the Hagen-Poiseuille equation, and for turbulent flow, the Darcy-Weisbach equation or empirical formulas like the Colebrook-White equation may be used. These calculations take into account factors such as fluid velocity, pressure loss, and pipe roughness.
Converting Between Different Pipe Size Standards
In various regions, different standards are used for pipe sizing, and you may need to convert between them:
Nominal Pipe Size (NPS) to Actual Diameter: NPS is a nominal designation and does not correspond directly to actual dimensions. For example, a 6-inch NPS pipe typically has an actual OD of approximately 6.625 inches, but the exact dimensions vary with the pipe schedule.
Diameter Nominal (DN) to NPS: To convert DN to NPS, you can use standard conversion tables or charts provided by pipe manufacturers. For example, DN100 is approximately equivalent to NPS 4 inches.
Pipe Schedule Conversion: To convert between different schedules, you need to account for the variations in wall thickness while maintaining the same nominal size. Pipe schedules are standardized, so you can refer to a pipe schedule chart to find equivalent dimensions.
In summary, accurately measuring and calculating carbon steel pipe sizes involves using the right tools, performing hydraulic calculations for flow rates, and converting between different sizing standards as needed. By following these steps, you can ensure that your pipes meet the necessary specifications and function effectively in your system.