Summary:
How to Safely Transport Sodium Methylate Solution: Key Guidelines and Tips
What is Sodium Methylate and Its Uses?
Essential Safety Precautions for Transporting Sodium Methylate Solution
Best Practices for Ensuring Safe Sodium Methylate Solution Transportation
Common Challenges and Solutions in Sodium Methylate Solution Transportation
Sodium methylate solution is an essential chemical used in various industries, including pharmaceuticals, biodiesel production, and chemical manufacturing. Because of its reactive nature and potential hazards, the transportation of this substance requires special attention and care. Understanding the importance of safe and effective transportation of sodium methylate is crucial for protecting both people and the environment.
What is Sodium Methylate and Its Uses?
Sodium methylate (NaOCH₃) is a chemical compound commonly found in the form of a solution. It’s typically used as a strong base in chemical reactions, particularly in the production of biodiesel, where it acts as a catalyst. It’s also used in the pharmaceutical industry for various syntheses, and in laboratories for chemical analysis. Given its diverse applications, sodium methylate is considered a valuable industrial chemical, but its handling requires meticulous safety protocols.
Why Safe Transportation of Sodium Methylate Solution is Crucial
When transporting sodium methylate solution, safety is paramount. The chemical is highly reactive, especially when in contact with water or acidic substances, which can result in dangerous reactions, including fires or the release of harmful gases. Improper handling or shipping of sodium methylate can lead to hazardous spills, environmental contamination, or even health risks to those involved in the transportation process.
Transporting sodium methylate safely is not just about following the rules; it’s about protecting lives and the environment. A spill or accident could cause severe harm, not only to the immediate surroundings but also to the broader ecosystem. Therefore, understanding the necessary safety measures and the regulatory requirements is essential for anyone involved in sodium methylate solution transportation.
Key Risks in Sodium Methylate Solution Transportation
There are several risks associated with the transportation of sodium methylate solution, making it a highly regulated chemical to ship. One of the primary concerns is its corrosive nature, which can cause severe damage to human skin and materials upon contact. In addition, mishandling of sodium methylate can lead to dangerous chemical reactions, especially when it comes into contact with moisture or other incompatible substances.
Another significant risk is the potential for leaks or spills, which can contaminate local water supplies or soil, leading to environmental damage. Because of these risks, it’s essential to ensure that proper containment and safety measures are in place throughout the transportation process. Additionally, extreme temperature changes during transit can also affect the stability of the sodium methylate solution, necessitating specific temperature-controlled conditions to avoid accidents.
Essential Safety Precautions for Transporting Sodium Methylate Solution
Transporting sodium methylate solution requires careful planning and strict adherence to safety protocols to avoid accidents and ensure compliance with regulatory standards. As a hazardous chemical, sodium methylate presents a number of safety challenges, which can be mitigated through proper safety measures. Below are key safety precautions that must be followed when transporting this solution.
Proper Packaging for Sodium Methylate Solution Transportation
The first line of defense when transporting sodium methylate solution is ensuring it is properly packaged. The container should be made of materials resistant to corrosion and able to withstand the chemical’s reactive nature. Typically, high-density polyethylene (HDPE) containers are used because they are durable and chemically resistant.
Moreover, the packaging should be designed to prevent leaks and spills. Double-sealed containers are often preferred, and any packaging should be designed with secondary containment features. These measures help to ensure that in the event of a minor leak or breakage, the chemical does not escape into the environment. Additionally, labeling the packaging with clear, prominent hazard warnings is crucial for ensuring that anyone handling the shipment understands the risks involved.
Choosing the Right Transport Vehicles for Safe Delivery
Selecting the correct transport vehicle is essential for the safe delivery of sodium methylate solution. The vehicle should be equipped with the proper safety equipment, such as spill kits, fire extinguishers, and emergency response tools, in case of an incident. Vehicles transporting sodium methylate should also be well-ventilated, as the solution can produce harmful vapors, especially if improperly stored or exposed to extreme conditions.
Furthermore, the vehicle must be able to safely carry the weight and volume of the solution while maintaining the correct temperature and pressure. Depending on the distance and route, some shipments may require temperature-controlled trucks to prevent any risk of chemical degradation. It’s essential to inspect the vehicle thoroughly before departure to ensure that there are no defects or damage that could compromise the safety of the shipment.
Labeling and Documentation Requirements for Sodium Methylate Shipments
Accurate and clear labeling is one of the most crucial safety precautions for transporting sodium methylate solution. The vehicle, packaging, and containers must all display the correct labels according to international regulations, such as the Globally Harmonized System (GHS) of Classification and Labeling of Chemicals. These labels should clearly indicate the hazardous nature of the contents and include proper safety symbols (e.g., corrosive, toxic) and emergency contact information.
In addition to the labeling, proper documentation is required for every shipment of sodium methylate solution. This includes a safety data sheet (SDS), which provides detailed information on the chemical’s properties, handling instructions, first aid measures, and emergency procedures. Transportation documents such as a bill of lading, shipping manifest, and any necessary permits must be in place to ensure compliance with local and international transport regulations.
Best Practices for Ensuring Safe Sodium Methylate Solution Transportation
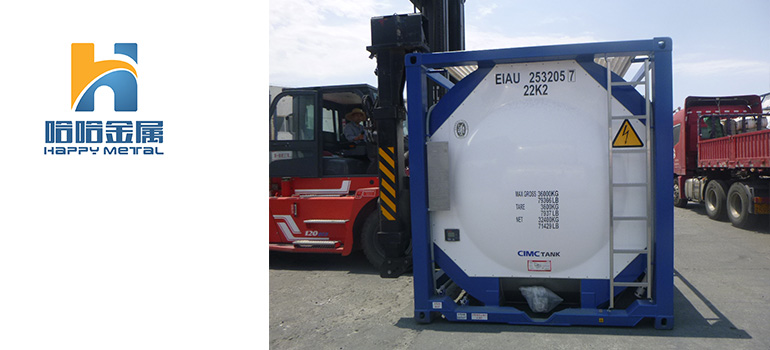
Ensuring the safe transportation of sodium methylate solution is a multifaceted process that requires careful planning, attention to detail, and adherence to best practices. By following established safety protocols and incorporating the latest industry standards, businesses can minimize risks, enhance efficiency, and protect both workers and the environment. Here are some best practices to ensure the safe transport of sodium methylate solution:
Monitoring and Tracking Sodium Methylate Shipments
One of the key best practices for transporting sodium methylate solution is the implementation of real-time monitoring and tracking systems. These systems allow you to monitor the shipment’s location, temperature, and other critical factors throughout the transportation process.
GPS Tracking: GPS tracking ensures that the shipment is on the correct route and helps reduce the chances of delays or detours. In the case of an emergency or incident, real-time location data enables swift responses to minimize damage or risks.
Environmental Monitoring: Sodium methylate is sensitive to temperature and humidity changes. Therefore, integrating temperature and humidity sensors within the shipment can help ensure the chemical is transported under optimal conditions. This is especially crucial for long-distance shipments or shipments that pass through extreme weather conditions.
Digital Logs: Using digital logs for each shipment helps maintain a record of all actions taken during the transportation process. These logs include data on handling, environmental conditions, and vehicle checks, making it easier to trace any problems back to their origin and address them quickly.
Temperature Control and Environmental Considerations
Sodium methylate solution is sensitive to extreme temperatures and environmental conditions. Proper temperature control is crucial to ensuring the stability and safety of the chemical during transit.
Temperature-Controlled Shipping: For sensitive shipments, it is essential to use temperature-controlled vehicles, especially for long shipments or routes that pass through areas with extreme heat or cold. Sodium methylate should be kept within a specific temperature range to prevent degradation or unwanted chemical reactions.
Environmental Hazards: In addition to temperature, environmental hazards like humidity, moisture, or exposure to sunlight can compromise the quality of sodium methylate. The shipping containers should be designed to protect the chemical from these environmental factors. Using moisture-resistant packaging and ensuring that the shipment is shielded from direct sunlight will help maintain the integrity of the solution.
Emergency Procedures in Case of Spills or Leaks
Despite all precautions, accidents can still happen, and having a clear and effective emergency response plan in place is essential. This plan should include procedures for handling leaks, spills, or accidents during transportation.
Spill Containment Kits: Vehicles used for transporting sodium methylate should always carry spill containment kits. These kits should include absorbent materials, neutralizing agents, and protective equipment to address any potential leaks. Quick containment is essential to limit exposure to sodium methylate and prevent environmental contamination.
Clear Communication: Drivers and handlers should have clear and easy access to emergency contact numbers and procedures. This ensures that if a spill or accident occurs, the appropriate authorities, such as local hazardous material response teams, can be contacted immediately.
Training and Drills: Regular training and emergency drills for employees involved in the transportation process are key. By training all personnel on the proper response to chemical spills, leaks, and other emergencies, businesses can reduce the impact of incidents and speed up response times.
Common Challenges and Solutions in Sodium Methylate Solution Transportation
Transporting sodium methylate solution comes with a unique set of challenges due to its hazardous nature and sensitivity to various environmental factors. Identifying these challenges and implementing appropriate solutions can help minimize risks, reduce delays, and ensure the safe delivery of the chemical. Below are some common challenges faced during sodium methylate solution transportation, along with effective solutions to address them.
Dealing with Delays and Disruptions in the Supply Chain
One of the most common challenges in transporting sodium methylate solution is dealing with delays in the supply chain. Delays can be caused by a variety of factors, such as road closures, customs issues, vehicle breakdowns, or unforeseen weather conditions. These disruptions can affect the timely delivery of the chemical and, in some cases, may compromise the stability or safety of the solution.
Solution: To mitigate delays, it’s crucial to plan the transportation route carefully. Use real-time tracking and GPS technology to monitor the shipment’s progress and adjust the route if needed. Establishing contingency plans, such as backup transportation options, can also ensure that any disruptions are addressed quickly. In addition, partnering with experienced logistics providers who specialize in hazardous material transport can reduce the risk of delays by ensuring compliance with all necessary regulations and safety standards.
Preventing Contamination and Degradation During Transport
Sodium methylate solution is highly reactive, and exposure to moisture, air, or extreme temperatures during transportation can lead to contamination or degradation of the chemical. If not properly controlled, these factors can compromise the quality of the solution and even lead to dangerous chemical reactions.
Solution: To prevent contamination and degradation, it’s essential to use high-quality, corrosion-resistant containers that are sealed tightly and designed to protect against moisture and air exposure. In addition, temperature control is critical, especially for long-distance shipments. Using temperature-controlled vehicles or insulated containers can help maintain the ideal temperature range for the solution. Additionally, always ensure that the packaging is clearly labeled with handling instructions to minimize the risk of mishandling or accidental exposure.
Managing the Risk of Spills or Leaks
Spills and leaks are an inherent risk when transporting hazardous chemicals like sodium methylate. Even with the best precautions, accidents can occur, leading to spills that may pose significant risks to both people and the environment. Sodium methylate is corrosive, and any exposure can cause serious harm to human health or damage to ecosystems.
Solution: The best way to manage the risk of spills is through proactive planning. Ensure that the containers used for transporting sodium methylate are double-sealed and made of durable materials like HDPE that are resistant to corrosion and chemical reactions. Additionally, transport vehicles should be equipped with spill containment kits that include absorbent materials, neutralizing agents, and personal protective equipment (PPE). Employees involved in the transportation process should be trained to respond quickly to spills, following established emergency protocols to minimize any damage.
Addressing Regulatory Compliance Challenges
The transportation of sodium methylate solution is subject to numerous local, national, and international regulations. Ensuring compliance with these regulations can be a challenge, especially when shipping across borders or dealing with varying legal requirements. Failing to comply with regulations can result in fines, delays, and even the confiscation of shipments.
Solution: To overcome regulatory challenges, it is vital to stay up-to-date with the latest laws and standards governing hazardous materials transportation. Familiarize yourself with regulations such as the IMDG Code, IATA Dangerous Goods Regulations, and DOT Hazardous Materials Regulations. This knowledge will help ensure that the proper documentation, labeling, and packaging standards are met. Collaborating with logistics providers who specialize in the transport of hazardous materials can also help ensure that all regulatory requirements are followed, reducing the risk of compliance issues.
Cost Management in Hazardous Material Transportation
Transporting sodium methylate solution can be expensive, especially when taking into account the costs associated with specialized packaging, temperature control, insurance, and regulatory compliance. Managing these costs while ensuring safe transportation can be challenging, particularly for smaller businesses with limited budgets.
Solution: Cost management can be achieved by optimizing transportation routes to reduce mileage and fuel costs, using efficient packaging that minimizes waste, and leveraging bulk shipping options. While it may seem like an upfront investment, choosing high-quality, durable packaging and temperature-controlled vehicles can prevent costly accidents or product degradation down the line. Additionally, businesses should work closely with logistics partners to negotiate rates and explore opportunities for cost-effective yet safe transportation solutions.