Summary:
How to Choose the Right Carbon Steel Pipe Sizes for Your Project
What Are Carbon Steel Pipe Sizes?
How to Select the Right Carbon Steel Pipe Sizes for Different Applications?
The Impact of Carbon Steel Pipe Sizes on Project Efficiency and Cost
Before selecting the right carbon steel pipe sizes for your project, it’s essential to understand the fundamentals of pipe sizing. The correct choice of carbon steel pipe sizes can significantly impact the quality, cost, and long-term efficiency of your project. In this section, we will explain what carbon steel pipe sizes are, how they are determined, and the common standards and classifications that can guide your decision-making process.
What Are Carbon Steel Pipe Sizes?
Carbon steel pipe sizes refer to the outside diameter (OD) and wall thickness (WT) of a pipe. These dimensions determine the strength, pressure capacity, flow rate, and suitability for various applications. Whether you’re working on a construction site or an industrial facility, choosing the correct carbon steel pipe size is crucial for ensuring safe and efficient fluid, gas, or material transport.
The two main ways carbon steel pipe sizes are described are Nominal Pipe Size (NPS) and Outside Diameter (OD). NPS is an approximate value that reflects the internal diameter of the pipe, while OD refers to the actual external diameter. The pipe’s wall thickness is often specified by its Schedule number, which defines the pipe’s pressure rating and resistance to corrosion or wear.
Key Factors That Determine Carbon Steel Pipe Sizes
When selecting carbon steel pipe sizes for a project, several key factors need to be considered:
Flow Requirements: The size of the pipe directly impacts the flow rate and velocity of the fluid. If the pipe is too small, it can cause restricted flow or even blockages. On the other hand, using an oversized pipe may lead to unnecessary costs and material waste.
Pressure Requirements: Different projects have varying pressure needs. Larger pipes are typically needed to handle higher pressure. The wall thickness (defined by the Schedule number) plays a crucial role in determining a pipe’s ability to withstand pressure.
Environmental Conditions: The environment in which the pipes will be installed affects size selection. For example, high temperatures, corrosive substances, or extreme physical conditions may require thicker walls or special coatings to maintain the pipe’s integrity.
Fitting and Installation Compatibility: It’s essential to choose pipe sizes that align with the installation requirements and compatible fittings. Some equipment or connection types may have specific size requirements, so selecting the right pipe size ensures proper compatibility with other system components.
Common Standards for Carbon Steel Pipe Sizes
Choosing the correct carbon steel pipe size also involves following industry standards. Various global standards exist to ensure the reliability and safety of pipes used across different sectors. Some of the most commonly used carbon steel pipe size standards include:
ASTM (American Society for Testing and Materials): ASTM A106 and ASTM A53 are widely used standards for carbon steel pipes, especially in the oil, gas, and fluid transportation industries. These standards define the size, pressure rating, and material properties of carbon steel pipes.
ANSI/ASME (American National Standards Institute / American Society of Mechanical Engineers): Standards like ASME B36.10 and ASME B36.19 provide detailed guidelines on carbon steel and stainless steel pipe sizes, wall thicknesses, and joining methods.
API (American Petroleum Institute): API 5L is the primary standard used in the oil and gas industry for pipeline construction. It outlines specifications for the size and strength of pipes used in the transportation of petroleum and natural gas.
These standards ensure that carbon steel pipes meet the required performance, safety, and compatibility standards for their specific applications. Therefore, when selecting pipe sizes, it’s important to check that they conform to the relevant industry specifications.
How to Select the Right Carbon Steel Pipe Sizes for Different Applications
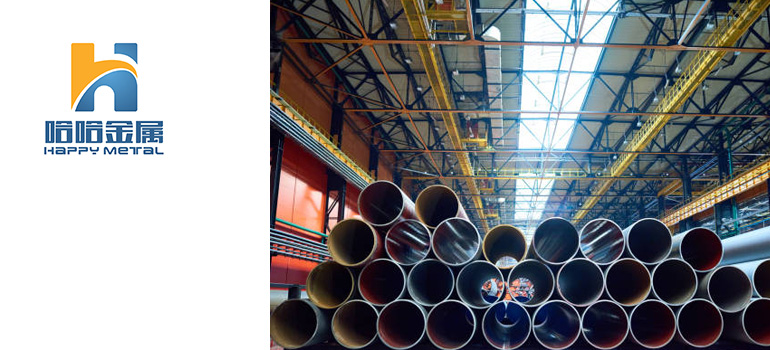
Selecting the right carbon steel pipe sizes for your project is critical to ensuring both efficiency and safety, as well as meeting the functional requirements of your specific application. Whether you’re working on a residential plumbing system, an industrial facility, or a large-scale oil and gas project, choosing the right pipe size can make all the difference in terms of performance, cost, and durability. In this section, we will guide you through how to select the right carbon steel pipe sizes for various applications, considering factors such as flow rate, pressure, and environmental conditions.
Choosing Pipe Sizes for Residential Plumbing
When selecting carbon steel pipe sizes for residential plumbing, several key factors must be considered, such as water flow demand, pipe material compatibility, and the layout of your plumbing system. In residential applications, the goal is to ensure a steady, sufficient supply of water while minimizing waste and avoiding pressure loss.
Flow Rate and Pressure Requirements: Typically, for residential systems, 1/2-inch to 1-inch carbon steel pipes are commonly used for standard plumbing lines. However, for larger homes or multi-story buildings, 1.5-inch to 2-inch pipes may be required to accommodate higher water flow and pressure demands. The pipe size needs to be large enough to prevent pressure drop, but not so large that it causes water wastage or excess cost.
Pipe Length and Layout: The length of the piping and the number of fixtures connected to it can also affect the choice of pipe size. For longer pipe runs, you may need larger pipes to maintain adequate pressure and flow. Ensure that the selected carbon steel pipe size matches the water usage of all household fixtures like faucets, showers, and washing machines.
Carbon Steel Pipe Sizes for Industrial Projects
In industrial settings, choosing the right carbon steel pipe size is more complex, as the pipes are often designed to transport not only water but also chemicals, gases, or even steam at high pressures and temperatures. Carbon steel pipes in these industries must withstand tough conditions, and the right size ensures safe and efficient operations.
Flow and Pressure Requirements: In industrial applications, the diameter of the pipe is directly related to the amount of material being transported and the pressure under which it is being transferred. For example, 2-inch to 6-inch carbon steel pipes are common in medium to large industrial projects where moderate to high flow rates are required. Larger pipes, such as 8-inch or 10-inch sizes, may be necessary for extremely high-volume operations or when transporting materials over long distances.
Temperature and Corrosion Resistance: Industrial pipes often operate under extreme conditions, with exposure to high temperatures or corrosive chemicals. When selecting carbon steel pipe sizes, it’s crucial to consider the thickness of the pipe wall (Schedule) to ensure it can withstand these harsh conditions. For example, Schedule 40 or Schedule 80 pipes are commonly used, with Schedule 80 offering thicker walls for higher-pressure applications.
Sizing Carbon Steel Pipes for Oil and Gas Applications
Oil and gas pipelines are some of the most critical and demanding applications for carbon steel pipes. These pipes need to handle not only high pressures but also the transportation of various liquids, gases, and chemicals across vast distances. Correctly selecting the right carbon steel pipe size is vital for ensuring efficiency, safety, and regulatory compliance.
Large-Scale Pipeline Sizes: In oil and gas applications, carbon steel pipe sizes can range from 4 inches to 48 inches or larger depending on the transportation requirements. Smaller pipelines (4 to 8 inches) are typically used for local or low-pressure systems, while larger pipelines (12 to 48 inches) are used for high-volume, long-distance transmission lines.
Pressure, Flow, and Fluid Type: Pressure and flow rate are among the most important factors to consider. For instance, when transporting high-pressure gas or crude oil, carbon steel pipes with larger diameters and thicker walls (e.g., Schedule 160 or Schedule XXS) are necessary. The type of fluid being transported also impacts pipe selection, as gases and liquids have different flow characteristics and pressure requirements.
Carbon Steel Pipe Sizes for Fire Protection Systems
In fire protection systems, carbon steel pipes play a crucial role in maintaining water pressure and flow to fire sprinklers and other fire suppression systems. The choice of pipe size is vital for ensuring that the fire protection system delivers sufficient water flow and pressure during an emergency.
Standard Pipe Sizes for Fire Protection: For most commercial or industrial fire protection systems, 2-inch to 6-inch carbon steel pipes are typically used. The specific size depends on the number of sprinklers, the building’s layout, and the required flow rate.
Pressure and Durability: Fire protection systems must withstand high pressures and operate reliably for long periods. Carbon steel pipes in these systems should be selected with the appropriate Schedule number (typically Schedule 40 or Schedule 80) to ensure that they can handle the expected pressure loads without failing.
Selecting the right carbon steel pipe sizes for your specific application involves a careful balance of various factors, including flow rate, pressure requirements, temperature, and environmental conditions. Whether you’re working with residential plumbing, industrial systems, oil and gas pipelines,or fire protection systems, choosing the correct pipe size ensures your system operates efficiently and safely. By understanding the unique demands of each application and adhering to industry standards, you can make informed decisions that save time, money, and resources in the long run.
The Impact of Carbon Steel Pipe Sizes on Project Efficiency and Cost
When it comes to the selection of carbon steel pipe sizes for any project, the choice can have a significant impact on both the overall efficiency of the system and the project’s costs. While choosing the right size is essential to ensure proper functionality and safety, it also plays a critical role in determining the performance, long-term durability, and operating costs of the system. From residential plumbing to large-scale industrial pipelines, understanding the effects of pipe sizing can help streamline operations and avoid unnecessary expenses.
In this section, we will explore how the carbon steel pipe sizes you choose can influence project efficiency and cost, and why it’s essential to make informed decisions at the outset of your project.
The Role of Pipe Sizes in Project Efficiency
Proper pipe sizing is crucial to ensuring the system operates at peak efficiency. Choosing the wrong carbon steel pipe size—whether it’s too small or too large—can lead to inefficiencies that affect the entire system, resulting in unnecessary energy consumption, maintenance costs, or safety risks.
Flow Rate and Pressure Loss
The most direct way in which carbon steel pipe sizes affect efficiency is through their influence on flow rates and pressure loss. If the pipe is too small for the required flow, the system may experience a pressure drop or restricted flow, leading to inefficient operation. This can require additional pumps or compressors to maintain the desired flow rate, which increases energy consumption.
Smaller Pipes: If pipes are undersized for the volume of fluid they need to carry, friction and resistance increase, leading to higher energy requirements to push the fluid through the system. This results in decreased system efficiency.
Larger Pipes: On the other hand, pipes that are too large may lead to inefficient flow velocities, especially when dealing with fluids that need to be transported at a specific velocity. While larger pipes can accommodate higher flow rates, they can also create water hammer issues or lead to wasted space in the system.
The Impact of Carbon Steel Pipe Sizes on Project Costs
The costs associated with selecting the wrong carbon steel pipe sizes can be substantial. Whether you’re underestimating the required pipe size or overestimating it, the long-term consequences can be costly in terms of both installation and operation.
Initial Material and Installation Costs
One of the most straightforward ways carbon steel pipe sizes impact project costs is through material and installation expenses. Larger pipes typically cost more in terms of both materials and labor. Oversized pipes require more welding, additional fittings, and larger supports, all of which can significantly increase installation costs.
Long-Term Operating Costs
Over time, improper pipe sizing can lead to increased energy costs or maintenance expenses. For instance, pipes that are too small may require the use of more energy-intensive pumps or compressors to push fluids through the system. On the other hand, overly large pipes can cause low flow velocity, leading to stagnation, sediment buildup, or potential corrosion issues, all of which result in higher maintenance costs.
Maintenance and Repair Costs
When pipes are too small or too large for their applications, there is a higher likelihood of wear and tear on the system, which can lead to costly repairs and maintenance. For instance, pipes that are undersized may suffer from increased friction or pressure, leading to early deterioration, while oversized pipes may experience slower flow velocities, increasing the likelihood of issues such as sediment buildup or corrosion.
Material Costs and Waste Reduction
In addition to labor and installation expenses, carbon steel pipe sizes can also affect material costs. Choosing pipes that are too large can result in material waste, which increases the overall cost of the project.
Material Waste:
When you select oversized pipes, you’re not only paying for extra material but also dealing with increased transportation and handling costs. Additionally, if the piping system is too large for the flow requirements, you could end up with unused portions of the pipe, which could result in scrap material or inefficient use of resources.
On the flip side, selecting the correct carbon steel pipe size ensures minimal waste. Pipe sizes that match the required flow rate and pressure will avoid unnecessary material costs while also keeping the project on budget. This is especially critical for large-scale industrial projects, where material costs can account for a significant portion of the total budget.
The carbon steel pipe sizes you choose can have a profound impact on both the efficiency and cost of your project. Whether you’re managing a residential plumbing system or a large-scale industrial pipeline, it’s crucial to strike the right balance between pipe size, material costs, operational efficiency, and long-term performance. By selecting the correct pipe sizes from the beginning, you can prevent unnecessary expenses, ensure smooth system operation, and avoid costly repairs and maintenance down the road.
By taking the time to carefully evaluate your needs and understanding the implications of pipe sizing on both efficiency and costs, you can make well-informed decisions that benefit your project in both the short and long term.