Summary:
The Advantages of Using Rolled Metal Plates in Construction and Manufacturing
Benefits of Rolled Metal Plates in Construction
Applications of Rolled Metal Plates in Manufacturing
How Rolled Metal Plates Improve Safety in Construction
The Role of Rolled Metal Plates in Sustainability and Eco-Friendly Practices
Why Rolled Metal Plates Are the Preferred Choice for Contractors and Manufacturers
Benefits of Rolled Metal Plates in Construction
Rolled metal plates, often referred to as flat steel or sheet metal, have become essential materials in the construction industry. Their versatility, strength, and cost-effectiveness make them a go-to choice for a wide range of applications, from structural frameworks to finishing touches on buildings. Below are some of the key benefits that rolled metal plates bring to the construction world.
Durability and Strength of Rolled Metal Plates in Structural Applications
One of the most significant advantages of rolled metal plates in construction is their durability and strength. When used as structural components, such as in beams, columns, or load-bearing walls, rolled metal plates offer superior support and stability. The rolled metal plate manufacturing process ensures a smooth, uniform surface that can withstand extreme forces, making it ideal for high-stress environments.
For example, in the construction of bridges or skyscrapers, where safety is paramount, the ability of rolled metal plates to bear weight without warping or degrading over time is critical. Thanks to their mechanical properties, rolled metal plates are resistant to fatigue and wear, providing long-term reliability in structural applications.
Cost-Effectiveness of Rolled Metal Plates for Large-Scale Projects
Another compelling reason for choosing rolled metal plates in construction is their cost-effectiveness. Compared to other materials like cast iron or forged steel, rolled metal plates are relatively affordable, particularly for large-scale projects. This is because the production process of rolled metal plates is efficient and scalable, allowing manufacturers to produce large quantities at a lower cost.
For contractors working on tight budgets or large construction projects, the affordability of rolled metal plates helps reduce overall project expenses while maintaining high quality and structural integrity. Additionally, the versatility of these plates means that they can be used in a wide range of applications, further increasing their cost-effectiveness.
Corrosion Resistance of Rolled Metal Plates in Harsh Environments
Construction projects often take place in environments where materials are exposed to harsh weather conditions, including moisture, salt, and extreme temperatures. Here, the corrosion resistance of rolled metal plates shines. Many rolled metal plates are treated with special coatings or made from alloys that offer resistance to rust and corrosion.
For instance, rolled metal plates made from stainless steel or galvanized steel can be used in coastal areas where saltwater exposure is a concern. These coatings help ensure the longevity of the plates, reducing maintenance costs and improving the durability of the structures they support. Whether in marine construction, outdoor buildings, or industrial facilities, corrosion-resistant rolled metal plates provide an essential defense against the elements.
In conclusion, the use of rolled metal plates in construction offers significant advantages in terms of strength, cost savings, and longevity. From their ability to bear heavy loads and provide structural integrity to their affordability for large-scale projects and resistance to corrosion, rolled metal plates are indispensable in modern construction. Whether you’re building bridges, skyscrapers, or residential homes, incorporating rolled metal plates into your project can ensure both reliability and cost-efficiency.
Applications of Rolled Metal Plates in Manufacturing
Rolled metal plates have revolutionized the manufacturing industry due to their remarkable versatility, high strength, and cost-effectiveness. These flat sheets of metal are used across a wide range of industries, from heavy machinery to automotive production. In manufacturing, rolled metal plates serve as the backbone for producing complex machinery, essential components, and structural elements that require durability and precision.
Use of Rolled Metal Plates in Heavy Machinery Production
In the manufacturing of heavy machinery, such as cranes, excavators, and industrial robots, rolled metal plates are crucial components. These large machines are subject to significant wear and tear, which requires materials that can withstand constant stress, pressure, and heavy loads. Rolled metal plates provide the strength and toughness needed for such applications.
For example, in the production of excavators, rolled metal plates are used to form the machine’s frame, which must endure immense stress while performing under demanding conditions. The uniform thickness and tensile strength of rolled metal plates make them ideal for creating machine components that need to support heavy weights and maintain structural integrity over time. Additionally, the high level of precision involved in the rolling process ensures that these metal plates can be shaped to exact specifications, which is essential for maintaining the performance and safety of heavy machinery.
How Rolled Metal Plates Improve Precision in Automotive Manufacturing
In the automotive industry, rolled metal plates are integral to the production of car bodies, engine components, and structural elements. Automotive manufacturers rely on the ability to shape and form metal plates into intricate designs without compromising strength or durability. Rolled metal plates, particularly those made from high-strength steel or aluminum alloys, are ideal for these tasks.
For instance, rolled metal plates are used to create the outer body panels of vehicles, where precision and smooth surfaces are essential. The process of rolling metal ensures that the thickness and properties of the plates are uniform, allowing manufacturers to produce parts that fit together seamlessly. Furthermore, the flexibility of rolled metal allows for easy stamping and shaping, which are essential steps in the automotive production line.
Another significant application is in the production of engine parts, where rolled metal plates can be used to create components such as engine blocks, pistons, and transmission housings. The high mechanical strength of these plates ensures that engine parts are able to withstand the extreme conditions inside an operating engine, including high temperatures and pressure.
Rolled Metal Plates for High-Quality Tooling and Equipment
In precision manufacturing, tooling and equipment are critical to ensuring that parts are produced with the highest level of accuracy. Rolled metal plates are often used to create specialized tooling, jigs, and fixtures that hold parts in place during machining processes.
For example, when creating molds for injection molding or die-casting processes, rolled metal plates are often the material of choice due to their ability to retain shape under high stress. These plates are also used to produce other tooling components like cutting tools, dies, and machine frames. The uniformity and strength of rolled metal plates allow manufacturers to create tools that can operate under high pressure and maintain their shape over repeated use, ensuring precise and consistent results in mass production.
Applications in Electrical and Electronics Manufacturing
In addition to heavy industries, rolled metal plates are also used extensively in the production of electrical and electronic components. These plates are used for creating heat sinks, electrical enclosures, and circuit boards. The excellent thermal conductivity of materials like aluminum and copper, when rolled into thin plates, allows for the efficient dissipation of heat in high-performance electronics and power devices.
For instance, in the production of heat sinks for computer processors, rolled metal plates made of aluminum are often used to absorb and dissipate the heat generated by the electronic components. The thin, flexible nature of these plates ensures that they can be easily customized into the required shapes for a variety of electronic devices, from consumer electronics to industrial machinery.
In summary, rolled metal plates play a pivotal role in the manufacturing industry, with applications ranging from heavy machinery production to the precision engineering of automotive parts and tooling equipment. Their strength, precision, and cost-effectiveness make them indispensable in producing a wide array of components used in diverse industries. Whether it’s for creating durable machinery, precise automotive components, or advanced electronics, the flexibility and reliability of rolled metal plates ensure their continued importance in modern manufacturing.
How Rolled Metal Plates Improve Safety in Construction
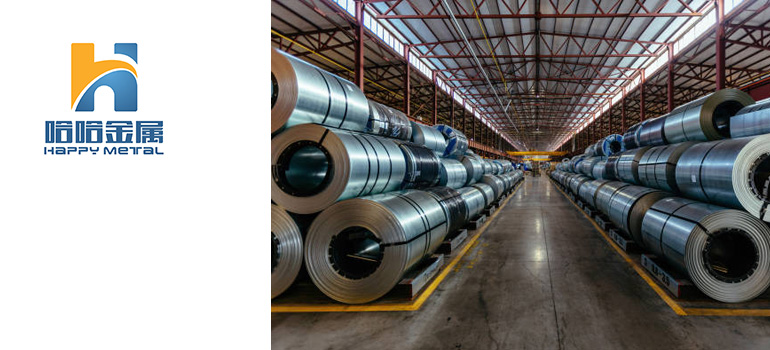
Safety is one of the top priorities in any construction project. Whether building skyscrapers, bridges, or residential homes, ensuring the stability and strength of the structure is crucial for protecting workers and occupants alike. Rolled metal plates, with their exceptional strength, durability, and versatility, play a significant role in enhancing construction site safety. By providing robust structural support, reducing the risk of failure, and meeting high standards of fire resistance, these materials help prevent accidents and ensure the long-term safety of the buildings.
Enhanced Structural Integrity with Rolled Metal Plates
One of the key ways rolled metal plates improve safety in construction is by enhancing the structural integrity of buildings. When used in the framework of structures, such as beams, columns, and load-bearing walls, rolled metal plates provide superior strength and load-bearing capacity. These metal plates are made through a precise rolling process, which ensures a uniform thickness and consistent material properties, essential for maintaining stability under heavy loads.
For example, in the construction of multi-story buildings or bridges, rolled metal plates are used to create support beams that bear the weight of the entire structure. Their ability to distribute weight evenly and resist deformation ensures that these critical components do not fail under stress, thereby reducing the risk of accidents due to structural collapse. The use of rolled metal plates for reinforcement in high-rise construction significantly minimizes the chances of structural failure during the building’s lifetime, which is crucial for both the construction crew and future occupants.
Fire Resistance of Rolled Metal Plates in Building Construction
Another important safety benefit of rolled metal plates is their fire resistance. Construction materials must meet strict fire safety standards, and many rolled metal plates—especially those made from materials like stainless steel or galvanized steel—offer excellent fire resistance properties. This is particularly important in high-rise buildings, industrial facilities, and other environments where fire hazards are a concern.
For example, in the event of a fire, rolled metal plates can help contain flames and prevent the spread of fire from one part of the building to another. Steel and other rolled metal plates are non-combustible, which means they won’t catch fire or contribute to the fire’s spread. They can also provide crucial fire barriers, protecting both the structure and the people inside. Rolled metal plates can be used in fireproofing systems, such as fire-resistant walls, floors, and ceilings, thereby significantly enhancing the overall fire safety of the building.
In addition, fire-resistant rolled metal plates help protect structural elements from the damaging effects of heat exposure, ensuring that the building remains structurally sound in the event of a fire. This capability can make a significant difference in preventing injuries or fatalities caused by structural collapse during a fire emergency.
Corrosion Resistance and Longevity for Safer Long-Term Use
Corrosion is a serious threat to construction materials, especially in environments exposed to moisture, salt, or extreme weather conditions. The corrosion of metal components can weaken the structural integrity of a building, leading to safety hazards. Rolled metal plates, however, are often coated or made from corrosion-resistant alloys, such as stainless steel or galvanized steel, ensuring that the material remains strong and durable over time.
For example, buildings located in coastal regions or industrial areas are exposed to harsh conditions that can lead to accelerated corrosion of materials. The use of corrosion-resistant rolled metal plates ensures that the structural components retain their strength, preventing premature wear and failure. This is particularly important in the case of support structures like beams and columns, which need to maintain their load-bearing capacity over many years.
By reducing the risk of material degradation due to corrosion, rolled metal plates enhance the safety of buildings and reduce the likelihood of costly repairs or structural failures. Regular maintenance of these plates can further extend their lifespan, contributing to long-term safety.
Seismic Safety with Rolled Metal Plates
In seismic-prone areas, rolled metal plates can significantly contribute to a building’s ability to withstand earthquakes. The ductility and flexibility of rolled metal plates, especially those made from high-strength steel alloys, allow buildings to absorb and dissipate seismic forces more effectively. This can prevent structural damage during an earthquake and reduce the likelihood of building collapse.
In earthquake-resistant construction, rolled metal plates are often used in the reinforcement of columns, beams, and foundation supports. These metal plates can help buildings resist lateral forces, such as those generated by ground shaking, and ensure the structural integrity of the building during seismic events. By incorporating rolled metal plates into the design of earthquake-resistant structures, builders can enhance the safety of the building and protect both the construction workers during construction and the occupants in the long term.
In conclusion, rolled metal plates play a crucial role in improving safety in construction projects. Their ability to enhance structural integrity, provide fire resistance, resist corrosion, and contribute to seismic safety makes them indispensable materials for modern construction. By using rolled metal plates in key structural elements, builders can significantly reduce the risks of accidents, improve the durability of the building, and ensure the safety of both construction workers and building occupants. With their strength, versatility, and reliability, rolled metal plates are a fundamental component of safe, sustainable construction practices.
The Role of Rolled Metal Plates in Sustainability and Eco-Friendly Practices
In the face of growing environmental concerns and stricter regulations, industries worldwide are seeking ways to minimize their ecological footprint. The construction and manufacturing sectors, which have traditionally been significant contributors to environmental degradation, are now adopting more sustainable materials and practices. Rolled metal plates, with their impressive versatility, durability, and recyclability, are playing an increasingly important role in these efforts. Not only do they contribute to more sustainable construction and manufacturing processes, but they also help reduce resource consumption and support eco-friendly design principles.
Recyclability of Rolled Metal Plates and Reduced Waste
One of the most significant environmental benefits of rolled metal plates is their high recyclability. Metals, particularly steel and aluminum, are among the most recycled materials in the world. Unlike many other construction materials, rolled metal plates can be recycled repeatedly without degrading their properties. This recyclability contributes significantly to reducing waste and minimizing the demand for virgin materials.
In construction, recycled rolled metal plates are used to create new structural components, reducing the need to mine and process raw metals, which is an energy-intensive process. By reusing metals from demolished buildings or industrial processes, construction projects can significantly lower their environmental impact. For example, rolled steel plates from old buildings can be melted down, refined, and rolled again into new plates for use in modern construction, leading to a circular economy where materials are reused rather than disposed of.
Energy Efficiency in Manufacturing with Rolled Metal Plates
The production of rolled metal plates itself has become increasingly energy-efficient, thanks to advances in manufacturing technologies. Modern rolling mills are designed to minimize energy consumption and reduce emissions, making the production process more eco-friendly. The ability to produce rolled metal plates with a lower energy input compared to traditional methods helps manufacturers reduce their overall carbon footprint.
Furthermore, once in use, rolled metal plates contribute to energy efficiency in buildings and machinery. In construction, rolled metal plates are often incorporated into energy-efficient designs, such as insulated walls, energy-efficient roofs, and reflective building facades that reduce heat absorption. For example, reflective metal panels can be used in the construction of roofs or facades to reduce the amount of heat absorbed by buildings, lowering the need for air conditioning and reducing energy consumption in warm climates. Similarly, rolled metal plates are used in HVAC systems, where they help improve the performance of energy-saving technologies by providing strong yet lightweight components.
Long Lifespan and Durability: Reducing the Need for Replacement
The durability of rolled metal plates is another key factor in their sustainability credentials. Metal plates, particularly those made from high-strength alloys, are designed to withstand harsh environmental conditions, including extreme temperatures, moisture, and corrosive environments. This long lifespan reduces the need for frequent replacements, leading to less waste and fewer resources spent on repair and replacement.
In the context of construction, rolled metal plates are often used in the framing and exterior cladding of buildings, where their resistance to weathering and corrosion helps extend the life of the structure. For example, galvanized steel plates are commonly used for roofing, siding, and structural components in buildings exposed to moisture or saltwater, such as coastal areas or industrial zones. Their ability to resist corrosion ensures that the materials do not need to be replaced as frequently, reducing the environmental impact associated with demolition and rebuilding.
Supporting Green Building Certifications and Eco-Friendly Design
The use of rolled metal plates also plays a crucial role in supporting green building certifications, such as LEED (Leadership in Energy and Environmental Design) and BREEAM (Building Research Establishment Environmental Assessment Method). These certifications encourage sustainable building practices by awarding points for environmentally friendly materials, energy-efficient designs, and low-impact construction methods.
Since rolled metal plates can be produced using recycled materials, and their durability and energy efficiency contribute to a building’s overall environmental performance, they are a valuable component in the design of eco-friendly buildings. Additionally, metal roofing systems made from rolled metal plates are often a key element in achieving sustainability goals, as they provide long-term durability while reducing the energy consumption of a building.
Reducing Carbon Emissions in Manufacturing
As manufacturers strive to reduce their carbon emissions, many are turning to rolled metal plates made from low-carbon steel or other innovative alloys. These materials are produced using more sustainable processes, which release fewer greenhouse gases than traditional methods. In addition, the use of rolled metal plates made from recycled metals further reduces carbon emissions, as the recycling process requires far less energy than producing metal from ore.
By incorporating rolled metal plates into manufacturing processes, industries can significantly reduce their carbon footprint and move closer to meeting their environmental targets. This is particularly important in industries such as automotive manufacturing, aerospace, and heavy machinery, where metal components are essential but can often contribute to high carbon emissions during production.
In conclusion, rolled metal plates are playing an essential role in advancing sustainability and eco-friendly practices across various industries. Their recyclability, energy efficiency, durability, and long lifespan make them ideal materials for reducing waste, conserving energy, and minimizing carbon emissions. Whether used in construction, manufacturing, or machinery, rolled metal plates support eco-friendly designs and sustainable practices, helping industries meet their environmental goals while also improving performance and reducing costs. As industries continue to embrace greener alternatives, rolled metal plates will remain a cornerstone of sustainable manufacturing and construction, contributing to a more environmentally responsible future.
Why Rolled Metal Plates Are the Preferred Choice for Contractors and Manufacturers
In the world of construction and manufacturing, selecting the right materials is crucial to the success of any project. When it comes to strength, durability, cost-effectiveness, and versatility, rolled metal plates stand out as the preferred choice for many contractors and manufacturers. These metal plates, produced through a specialized rolling process, are used in everything from structural elements in buildings to components in heavy machinery and vehicles. Their wide range of benefits makes them an essential material in various industries, providing the perfect combination of performance and value.
Versatility of Rolled Metal Plates Across Different Applications
One of the key reasons rolled metal plates are favored by contractors and manufacturers is their versatility. These plates come in a variety of thicknesses, sizes, and metal alloys, which makes them suitable for a broad range of applications. Whether it’s in the construction of high-rise buildings, bridges, industrial equipment, or automotive parts, rolled metal plates can be adapted to meet specific project requirements.
For example, in construction, rolled metal plates are used for structural components like beams, columns, and supports due to their high tensile strength and ability to bear heavy loads. In manufacturing, they are used in everything from machinery frames to precision tooling. The ability to customize rolled metal plates for such varied uses allows contractors and manufacturers to choose the best material for their specific needs, ensuring high-quality results across all stages of production.
In the automotive industry, rolled metal plates are used to create body panels, engine components, and exhaust systems, where strength, weight, and durability are crucial. The flexibility and uniformity of rolled metal plates allow manufacturers to produce parts with high precision, resulting in better-fitting components and improved overall product quality.
Strength and Durability of Rolled Metal Plates in Heavy Applications
Another significant reason rolled metal plates are the preferred choice is their strength and durability. Unlike other materials, rolled metal plates can withstand the immense pressures and stresses encountered in industrial and construction applications. Whether used for structural support in buildings or as critical components in machinery, these plates offer excellent performance over time.
In construction, rolled metal plates provide structural integrity that is vital for the safety of the building. High-strength steel plates, for example, are often used in bridges, high-rise buildings, and other load-bearing structures due to their ability to handle heavy loads and resist deformation. This durability means that rolled metal plates can perform reliably over long periods, even in demanding environments, reducing the need for frequent repairs or replacements.
For contractors, the use of rolled metal plates ensures that the materials used in their projects are not only strong but also able to withstand wear and tear from harsh weather conditions or heavy machinery. For example, galvanized steel plates are used in applications where resistance to rust and corrosion is crucial, such as in coastal regions or industrial environments exposed to chemicals or saltwater.
Cost-Effectiveness of Rolled Metal Plates for Large-Scale Projects
The cost-effectiveness of rolled metal plates is another key factor in their popularity among contractors and manufacturers. The production process for rolled metal plates is highly efficient, allowing manufacturers to produce large quantities of plates at lower costs compared to other materials. This affordability makes rolled metal plates an attractive option for large-scale projects, where cost considerations play a critical role.
For contractors working on budget-conscious projects, such as public infrastructure or commercial buildings, using rolled metal plates can help keep material costs low without sacrificing strength or quality. The economical nature of rolled metal plates also extends to the construction process, as these plates are easy to handle, transport, and install, reducing labor and transportation costs.
In the manufacturing sector, the cost-effectiveness of rolled metal plates allows businesses to scale their operations and produce more parts for less. Since rolled metal plates are available in large sheets and can be cut or shaped into various forms, manufacturers can minimize material waste and improve overall cost efficiency, whether they’re making components for vehicles, machinery, or electronics.
Availability and Accessibility of Rolled Metal Plates in the Market
Another reason why rolled metal plates are the preferred choice for contractors and manufacturers is their availability and widespread use. Because they are produced in large quantities by numerous suppliers, rolled metal plates are easy to source and come in a range of grades, finishes, and dimensions. This widespread availability makes it easier for contractors to obtain the right material for their projects quickly, without long wait times or complicated sourcing.
In addition, suppliers of rolled metal plates offer customization options, such as cutting, bending, and coating, to meet the specific requirements of a project. This ensures that contractors and manufacturers receive exactly the right material for their needs, whether they require specific metal alloys or particular dimensions.
Long-Term Cost Savings with Rolled Metal Plates in Construction and Manufacturing
Finally, one of the key advantages of using rolled metal plates is their ability to provide long-term cost savings. Due to their durability and low maintenance needs, rolled metal plates can last for many years without needing extensive repairs or replacements. This reduces lifecycle costs and increases the overall value of the building or product.
For contractors, using rolled metal plates can translate into lower maintenance and repair costs, as the materials are resistant to corrosion, wear, and tear. This is particularly important in environments where buildings or machinery are exposed to extreme conditions, such as in coastal areas or heavy industrial settings.
Manufacturers also benefit from the long-term durability of rolled metal plates, as products made from these materials often require fewer repairs and last longer, leading to improved customer satisfaction and lower warranty costs.
In conclusion, rolled metal plates are the preferred choice for contractors and manufacturers because of their versatility, strength, durability, cost-effectiveness, and availability. These plates provide an optimal solution for a wide range of applications, from structural components in construction to precision parts in manufacturing. By offering the perfect balance of performance and value, rolled metal plate help contractors and manufacturers achieve high-quality results while keeping costs under control. Their ability to withstand harsh conditions and provide long-term performance makes them an indispensable material in both construction and manufacturing industries.