Summary:
Stainless Steel Pipes: The Key to Durability in Marine and Offshore Applications
The Importance of Durability in Marine and Offshore Environments
Key Benefits of Stainless Steel Pipes in Marine Applications
How Stainless Steel Pipe Applications Ensure Safety and Reliability in Offshore Projects
Types of Stainless Steel Used in Marine and Offshore Pipe Systems
The Importance of Durability in Marine and Offshore Environments
When it comes to marine and offshore applications, durability is more than just a desirable trait—it’s a critical factor that determines the success and longevity of an operation. Pipes in these environments are subjected to some of the harshest conditions on Earth, including extreme temperatures, high pressures, and the constant threat of corrosion from saltwater and other corrosive elements. As such, the materials used to construct these pipes need to be robust, long-lasting, and able to withstand the challenges posed by the marine and offshore environment.
Why Durability Matters in Marine and Offshore Applications
In both marine and offshore industries, whether it’s shipping, oil and gas extraction, or renewable energy projects, the reliability of pipe systems is paramount. These systems are responsible for transporting essential fluids—ranging from water and oil to natural gas and chemicals—under often extreme conditions. A failure in these systems can lead to costly downtime, environmental hazards, and even catastrophic safety incidents.
The high-stakes nature of these industries means that every piece of equipment, including pipes, must be built to endure continuous exposure to the elements. That’s why the durability of materials like stainless steel is so highly valued in marine and offshore applications. Stainless steel pipes are known for their exceptional strength and resistance to corrosion, ensuring that they maintain their structural integrity over time, even under the harshest conditions.
Environmental Challenges for Pipes in Marine Settings
Marine environments present unique challenges for pipes, as they are exposed to constant moisture, saltwater, and sometimes even the corrosive effects of marine life. Saltwater, in particular, is notorious for accelerating corrosion, which can quickly compromise the performance of pipes. In addition, pipes used in marine applications must also endure the physical stress of waves, storms, and constant motion, all of which put added pressure on the structural materials.
Beyond corrosion, marine pipes are also exposed to biological growth like barnacles and algae, which can accumulate on the surfaces and clog systems, reducing efficiency and increasing maintenance costs. These biological deposits can be especially problematic for pipelines used in water intake or cooling systems.
Moreover, marine environments are often subject to temperature fluctuations, from freezing cold water depths to the heat of tropical climates, and the pipes must be able to withstand this thermal stress without cracking or warping. The materials used must also endure high pressures, especially in offshore deepwater applications where pipes are deployed at great depths.
How Stainless Steel Pipes Overcome Corrosion and Wear
This is where stainless steel pipe applications truly shine. The unique alloy composition of stainless steel makes it inherently resistant to many forms of corrosion, especially the kind caused by saltwater and humidity. The chromium content in stainless steel forms a passive oxide layer on the surface, which acts as a protective barrier against corrosion. In environments like the ocean, where saltwater can wreak havoc on unprotected metals, this corrosion resistance is crucial for maintaining the longevity and integrity of the piping system.
In addition to corrosion resistance, stainless steel pipes are highly resistant to wear and tear caused by the constant movement of water, debris, and sediment. The strength of stainless steel ensures that even under high-pressure conditions—whether from deep-water offshore drilling operations or intense tidal forces—these pipes will remain structurally sound and continue to perform their functions.
Moreover, stainless steel’s ability to handle extreme temperatures without losing strength is another reason it’s so effective in marine and offshore applications. Whether exposed to freezing temperatures or the heat of machinery, stainless steel pipes maintain their form and functionality, contributing to greater reliability over time.
The Role of Durability in Reducing Maintenance and Operational Costs
Durability also plays a key role in reducing maintenance costs, which is an ongoing concern in marine and offshore operations. The high maintenance demands of traditional piping materials, such as carbon steel or copper, can be prohibitively expensive, particularly when maintenance crews must frequently inspect, repair, or replace damaged pipes. These pipes also require additional coatings or treatments to protect them from corrosion, which adds to the overall cost.
Stainless steel, on the other hand, often requires less frequent maintenance, thanks to its superior durability and corrosion resistance. This results in fewer replacements and repairs over the lifespan of the pipe, ultimately leading to lower operational costs. In offshore oil rigs or marine vessels, where downtime is costly and even a small failure can lead to significant financial losses, the reduced need for maintenance is an invaluable benefit.
In marine and offshore applications, where extreme conditions are the norm, stainless steel pipe applications stand out for their unmatched durability. These pipes provide the strength and resilience necessary to withstand corrosion, pressure, and physical wear, all while offering long-term reliability and cost savings. Whether it’s offshore oil rigs, desalination plants, or underwater pipelines, stainless steel is the material of choice for ensuring that the systems stay operational and safe for years to come. The durability of stainless steel pipes isn’t just about performance—it’s about maintaining the integrity of critical infrastructure and minimizing the risks that come with failures in these high-stakes environments.
Key Benefits of Stainless Steel Pipes in Marine Applications
Stainless steel pipes are widely regarded as one of the most reliable and durable materials for marine applications. Whether used in shipbuilding, offshore oil rigs, or underwater pipelines, stainless steel offers several key benefits that make it the material of choice for handling the tough conditions of the marine environment. Here, we’ll explore the top advantages that make stainless steel pipe applications essential for marine industries.
Superior Resistance to Corrosion and Saltwater
One of the most significant benefits of stainless steel pipes in marine applications is their exceptional resistance to corrosion, particularly from saltwater. Saltwater is one of the most corrosive substances, and metals exposed to the ocean are at constant risk of rust and degradation. Unlike carbon steel, which requires regular maintenance or coatings to prevent rust, stainless steel naturally forms a protective chromium oxide layer when exposed to oxygen, which prevents further corrosion. This built-in corrosion resistance makes stainless steel pipes ideal for submerged applications and helps extend the lifespan of marine infrastructure.
Whether it’s in the hulls of ships or underwater oil pipelines, stainless steel pipes are designed to withstand the harshest saltwater conditions, maintaining their integrity even after years of exposure.
Long Lifespan and Low Maintenance Costs
In the marine industry, the durability of materials is key to reducing operational costs. Stainless steel pipes are known for their long lifespan due to their resistance to corrosion, wear, and extreme weather conditions. Unlike other materials, stainless steel does not require frequent replacements or repairs, which leads to lower long-term maintenance costs.
For example, traditional materials like carbon steel or copper pipes might need regular replacement or treatment to prevent rust and degradation, but stainless steel requires far less maintenance over its lifetime. This reduced need for upkeep can translate into significant savings for businesses, especially in offshore and maritime operations where replacing or repairing pipes can be time-consuming and expensive.
Enhanced Strength and Pressure Resistance
Marine environments can involve extreme pressure conditions, especially in deep-water applications like offshore oil and gas drilling or underwater pipeline systems. Stainless steel pipes are known for their exceptional strength and ability to withstand high-pressure environments without compromising structural integrity. Whether it’s dealing with the high-pressure systems found in underwater oil rigs or the stress of constant water movement, stainless steel maintains its strength, ensuring that pipelines continue to function efficiently even under extreme conditions.
This level of strength is crucial in offshore environments, where pipes need to transport fluids and gases safely across vast distances, sometimes at depths where the pressure is immense. The ability of stainless steel to maintain its performance in these high-pressure environments makes it an ideal choice for critical infrastructure.
Resistance to Biological Fouling
In addition to the corrosive challenges posed by saltwater, marine pipes are also subject to biological fouling, which occurs when marine organisms such as barnacles, algae, and mollusks attach to the pipe surfaces. These organisms can block pipes, reduce efficiency, and increase maintenance requirements. Stainless steel is less susceptible to this type of fouling compared to other materials like copper or iron, which are more prone to biological buildup.
The smooth surface of stainless steel makes it more difficult for marine organisms to adhere, reducing the frequency and cost of maintenance. In applications where water intake or cooling systems are involved, this resistance to biological fouling is particularly beneficial, as it helps maintain the flow of water and reduces the need for cleaning.
High Temperature Tolerance
Marine and offshore applications are often subject to extreme temperature fluctuations, from cold waters in the deep sea to the heat generated by machinery on ships and rigs. Stainless steel pipes are highly resistant to temperature extremes, which allows them to perform consistently in both hot and cold environments. Whether it’s handling steam, hot water, or the freezing temperatures of the deep ocean, stainless steel pipes maintain their strength and resistance to deformation.
This temperature tolerance makes stainless steel ideal for a variety of marine applications, including HVAC systems on ships, water distribution systems on offshore platforms, and heat exchangers in marine environments. Unlike other materials that might warp or lose structural integrity in extreme temperatures, stainless steel remains stable and functional.
Sustainability and Environmental Benefits
In recent years, there has been a growing emphasis on sustainability and environmental responsibility in the marine industry. Stainless steel is not only durable but also recyclable, making it an environmentally friendly choice for marine applications. As industries strive to reduce their environmental footprint, choosing stainless steel pipes helps meet sustainability goals while maintaining operational efficiency.
Moreover, the longevity and reduced need for maintenance mean that stainless steel pipes contribute to a reduction in waste and resource consumption, which is an increasingly important consideration for industries working on environmentally sensitive projects such as offshore renewable energy or marine conservation.
The benefits of stainless steel pipes in marine applications are undeniable. From superior corrosion resistance and strength to long-term cost savings and sustainability, stainless steel offers unparalleled advantages in the harshest environments. Whether in shipbuilding, offshore oil rigs, or underwater pipelines, stainless steel remains the material of choice for industries seeking reliable, durable, and cost-effective solutions.
With its ability to withstand extreme pressures, resist corrosion, and handle temperature fluctuations, stainless steel ensures that marine infrastructure remains operational for years, helping businesses reduce maintenance costs and improve efficiency. As the marine industry continues to face environmental challenges, the demand for stainless steel pipe applications will only grow, solidifying its role as a key material in the sector’s future.
How Stainless Steel Pipe Applications Ensure Safety and Reliability in Offshore Projects
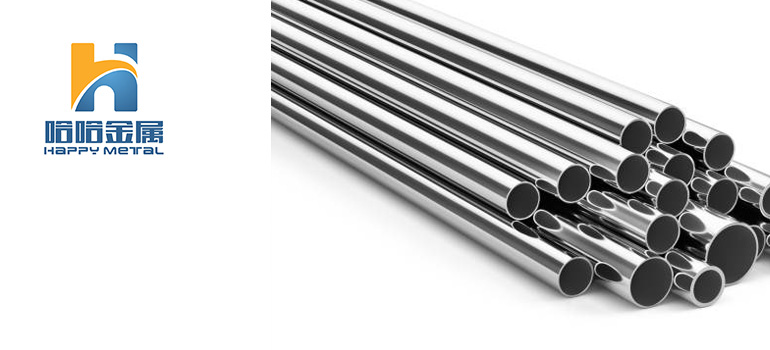
In offshore projects, safety and reliability are paramount. The challenging conditions of the open ocean—ranging from harsh weather to extreme pressures and corrosive saltwater—demand materials that not only meet stringent performance standards but also offer long-term dependability. Stainless steel pipe applications have proven to be indispensable in maintaining both safety and operational reliability in offshore industries, such as oil and gas extraction, marine transportation, and renewable energy.
Meeting Regulatory Standards and Safety Protocols
Offshore industries are subject to rigorous safety regulations designed to prevent accidents, environmental damage, and system failures. Stainless steel pipes, with their inherent strength and corrosion resistance, are often specified to meet or exceed these regulatory standards. These standards are critical because even minor failures in pipeline systems can lead to catastrophic consequences in offshore environments, such as oil spills, gas leaks, or explosions.
Stainless steel’s resistance to both physical stress and environmental degradation means that it consistently meets the stringent safety protocols required for offshore applications. For example, in offshore oil rigs, stainless steel pipes are essential for transporting oil, gas, and chemicals safely between platforms and storage facilities, ensuring no leaks or failures in highly sensitive areas.
The Role of Stainless Steel Pipes in Critical Offshore Systems
Offshore projects, particularly in the oil and gas industry, rely on complex pipe systems to transport fluids under high pressure and extreme temperatures. Stainless steel pipes play a key role in ensuring these systems remain operational, regardless of the demanding conditions. Their exceptional strength allows them to handle the high-pressure environments typically found in offshore drilling or production.
For instance, in deep-water drilling operations, where pipes are subject to immense pressure from the water column and the fluids being transported, stainless steel’s resistance to pressure-induced deformation is crucial. This makes stainless steel the material of choice for risers, pipelines, and valves that are involved in high-pressure fluid transport, ensuring the safety and continuous operation of offshore platforms.
Case Studies: Successful Use of Stainless Steel Pipes in Offshore Platforms
A great way to highlight the reliability of stainless steel pipes in offshore applications is through real-world examples. Offshore oil rigs, such as those in the North Sea and Gulf of Mexico, depend on stainless steel pipe applications for everything from water injection lines to fuel distribution systems. The ability of stainless steel to withstand both the aggressive offshore environment and the pressures of operation under deep-sea conditions has made it a proven solution.
One notable example is the use of stainless steel pipes in the subsea systems for oil extraction. These pipes not only need to endure the physical stresses of being submerged at great depths but also resist corrosion from saltwater, which can quickly degrade unprotected metals. Offshore operators report that stainless steel pipes significantly reduce the frequency of maintenance checks and system failures compared to alternatives, contributing to enhanced safety and overall operational reliability.
Additionally, in offshore wind farms, stainless steel pipes are used to support the infrastructure that holds turbines in place, as well as in the underwater cabling systems that connect turbines to the grid. Stainless steel’s durability and resistance to the constant wave motion and saltwater corrosion ensure that the structures remain intact and operational over the long term.
Reducing Risks of Contamination and Leaks
Offshore projects often handle hazardous materials, such as oil, natural gas, and chemicals, which can pose significant environmental and safety risks if pipes leak or rupture. Stainless steel pipes are resistant to cracking, which is particularly important in environments where materials like oil and gas are under high pressure. The smooth interior surface of stainless steel pipes also helps prevent blockages or contaminant buildup, further reducing the risk of leaks or system failures.
For example, in the transportation of oil and gas, even the smallest leak can lead to massive environmental disasters. Stainless steel’s durability and resistance to rupture make it a vital component in keeping offshore pipelines intact, reducing the likelihood of accidental discharges into the ocean. Moreover, the material’s ability to handle extreme pressure without losing its structural integrity is critical in avoiding leaks in high-risk zones.
Extended Lifespan and Reduced Maintenance Needs
In offshore environments, where accessing and repairing damaged pipes can be a costly and challenging task, stainless steel’s long lifespan significantly enhances safety and reliability. Unlike other materials, which may require frequent repairs or replacement due to corrosion, cracking, or material fatigue, stainless steel pipes require far less maintenance, even after years of service in harsh conditions.
This durability not only ensures that offshore systems run smoothly with minimal disruption but also minimizes the potential for system failures that could compromise safety. Fewer repairs mean less downtime and fewer opportunities for hazardous situations to develop. For offshore oil rigs or wind farms that operate in remote locations, this reduced need for maintenance is a major factor in keeping operations safe and continuous.
Enhancing Operational Efficiency
In offshore projects, every component must perform efficiently to ensure the success of the entire operation. Stainless steel pipes contribute to enhanced operational efficiency by maintaining optimal fluid flow and system integrity. Their resistance to corrosion and wear helps maintain the efficiency of transport systems, ensuring that fluids like oil, water, or gas move through the pipes without obstruction, leakage, or loss of pressure.
With stainless steel, offshore operations experience fewer disruptions due to system failures, which allows for continuous production and reliable output. This operational efficiency directly translates into improved safety, as all systems can work in sync without the threat of unforeseen issues that could endanger workers or the environment.
In offshore projects, where the stakes are high and the conditions are tough, stainless steel pipe applications offer unmatched safety, reliability, and performance. Their superior strength, resistance to corrosion, ability to handle extreme pressures, and minimal maintenance needs make them an essential part of offshore infrastructure. By ensuring the integrity of critical systems, reducing maintenance costs, and preventing the risks associated with leaks and failures, stainless steel pipes contribute to safer, more efficient offshore operations.
As offshore industries continue to evolve, the role of stainless steel pipes in maintaining operational excellence and safety will only become more crucial. From oil and gas platforms to offshore wind farms, the durability of stainless steel ensures that these projects remain secure and efficient, helping to protect both workers and the environment.
Types of Stainless Steel Used in Marine and Offshore Pipe Systems
Stainless steel is the material of choice for pipe systems in marine and offshore environments due to its strength, durability, and resistance to corrosion. However, not all stainless steels are the same—different grades of stainless steel offer unique properties that make them more suitable for specific applications. In marine and offshore industries, where pipes must withstand saltwater exposure, extreme temperatures, and high-pressure environments, selecting the right type of stainless steel is critical.
Here, we’ll explore the most common types of stainless steel used in marine and offshore pipe systems, highlighting their properties and specific applications.
Austenitic Stainless Steel (Grades 304 and 316)
Austenitic stainless steel is by far the most commonly used type in marine and offshore applications. Known for its excellent corrosion resistance and formability, this family of stainless steels is ideal for environments where durability and resistance to saltwater and atmospheric corrosion are critical.
Grade 304 Stainless Steel
Grade 304 is often used in less demanding marine applications. It offers good corrosion resistance in a variety of environments, including mild to moderately corrosive marine conditions. While 304 stainless steel is resistant to rust and oxidation, it is not as durable in harsh, high-salinity environments as grade 316. It is typically used for non-structural pipes, exhaust systems, and other equipment that are exposed to marine environments but are not subject to severe corrosion.
Grade 316 Stainless Steel
Grade 316 is the most widely used austenitic stainless steel in marine and offshore industries, particularly in highly corrosive environments. It contains molybdenum, which significantly improves its resistance to pitting and crevice corrosion in chloride-rich environments such as seawater. Grade 316 stainless steel is commonly used for marine pipes, offshore drilling equipment, heat exchangers, and water filtration systems, where resistance to saltwater corrosion is a primary concern.
Its superior resistance to corrosion, particularly in saltwater, and high levels of durability make 316 stainless steel ideal for high-performance applications, including subsea and offshore environments where reliability is crucial.
Ferritic Stainless Steel (Grade 430)
Ferritic stainless steel contains a high amount of iron, chromium, and low carbon content. It is magnetic and has good resistance to stress corrosion cracking but is not as resistant to oxidation and pitting as austenitic grades like 316. Ferritic stainless steel is not as commonly used in marine environments but can be found in some offshore applications where cost is a consideration, and the corrosion risk is lower.
Grade 430 Stainless Steel
Grade 430 is the most common ferritic stainless steel, and while it offers reasonable corrosion resistance, it is mainly used in applications where the material will not be exposed to highly corrosive environments. It is often used in applications where aesthetics or strength are more important than corrosion resistance, such as in some offshore construction components or marine equipment that do not come into direct contact with seawater.
While it is not as durable in aggressive marine environments as 304 or 316 stainless steel, it still has applications in areas where the risk of corrosion is moderate, such as cladding, decorative trim, or certain pressure vessels.
Duplex Stainless Steel (Grades 2205 and 2507)
Duplex stainless steel combines the benefits of both austenitic and ferritic stainless steels. These alloys have a two-phase microstructure that makes them exceptionally resistant to corrosion and stress corrosion cracking, while also providing high strength and toughness. Duplex stainless steel is particularly effective in marine environments where high strength is required alongside excellent corrosion resistance.
Grade 2205 Duplex Stainless Steel
Grade 2205 is one of the most common duplex grades used in marine and offshore applications. It has a higher resistance to pitting and crevice corrosion than standard austenitic steels like 304 and 316, making it suitable for environments exposed to saltwater and acidic conditions. It is often used in marine pipeline systems, offshore structures, and marine exhaust systems where both high mechanical strength and corrosion resistance are required.
Additionally, Grade 2205 is resistant to stress corrosion cracking, which is particularly important in marine and offshore environments subject to fluctuating temperatures and mechanical stresses.
Grade 2507 Super Duplex Stainless Steel
Grade 2507, a higher-alloyed version of duplex stainless steel, is known for its enhanced resistance to corrosion, pitting, and stress corrosion cracking in extremely harsh environments. It is typically used in subsea applications, offshore oil rigs, and chemical processing industries where even greater strength and resistance to aggressive marine conditions are required. The superior performance of 2507 makes it ideal for subsea pipelines, pressure vessels, and heat exchangers exposed to both chloride stress and high-pressure systems.
Precipitation-Hardening Stainless Steel (Grade 17-4 PH)
Precipitation-hardening stainless steel combines high strength and corrosion resistance with the ability to be hardened through heat treatment. These alloys are often used in applications where both strength and durability are essential. While not as commonly used as austenitic or duplex steels, precipitation-hardening stainless steels are found in some offshore applications that require specialized properties.
Grade 17-4 PH Stainless Steel
Grade 17-4 PH is one of the most commonly used precipitation-hardening stainless steels in offshore applications. It offers high strength and corrosion resistance, especially in offshore oil and gas exploration, valves, and high-performance marine structures. This material is often chosen for components that will undergo extreme mechanical stress or need to be resistant to both corrosion and high-impact wear.
It is not as resistant to pitting and crevice corrosion as austenitic grades like 316, but it offers superior strength, making it an excellent choice for structural components that also need to perform under high mechanical loads.
Choosing the Right Stainless Steel for Marine and Offshore Pipe Systems
When selecting stainless steel for marine and offshore pipe systems, the choice of material depends on several factors, including:
- Corrosion Resistance: The level of exposure to seawater or chemicals determines whether you need the enhanced corrosion resistance of 316 or a duplex alloy like 2205 or 2507.
- Mechanical Strength: For applications with high-pressure requirements, duplex and precipitation-hardening stainless steels provide superior strength.
- Cost and Performance: While 304 stainless steel is cost-effective and performs well in moderate conditions, 316 and 2205 are often the best choices for highly corrosive offshore environments despite their higher cost.
The variety of stainless steel grades available for marine and offshore pipe systems allows for precise selection based on environmental and operational conditions. Grade 316 is the most common choice for marine and offshore applications due to its outstanding resistance to corrosion, while duplex stainless steels like 2205 and 2507 offer superior strength and resistance to harsh conditions. By understanding the properties of each grade, offshore and marine industries can select the most appropriate material to ensure long-lasting, reliable performance in the toughest environments.