Summary:
Everything You Need to Know About Stainless Steel Pipe Standards
What are Stainless Steel Pipe Standards
Importance of Standardization in the Industry
Major Types of Stainless Steel Pipe Standards
Key Parameters Defined by Stainless Steel Pipe Standards
Compliance and Certification Processes
What are Stainless Steel Pipe Standards?
Imagine stainless steel pipe standards as the blueprints that govern every aspect of stainless steel pipe production and use. Just like a recipe ensures a consistent dish every time it’s followed, these standards outline the precise ingredients (chemical composition), cooking techniques (manufacturing processes), and quality checks (testing procedures) needed to produce pipes that meet specific performance requirements.
Importance of Standardization in the Industry
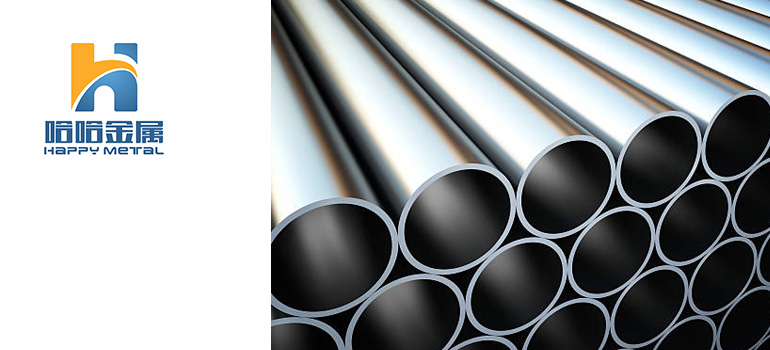
Standardization plays a pivotal role in the industry, particularly in sectors like manufacturing, construction, and engineering where precision, reliability, and safety are paramount. Here are some key reasons why standardization is crucial:
Quality Assurance: Standards establish uniform benchmarks for product quality and performance. By adhering to standardized processes and specifications, manufacturers can consistently produce goods that meet or exceed customer expectations. This reliability builds trust and confidence among consumers and stakeholders.
Interoperability and Compatibility: Standards ensure that products and components from different manufacturers are compatible and can work together seamlessly. In industries like electronics, automotive, and information technology, standardized interfaces and protocols enable interoperability, fostering innovation and enabling diverse applications.
Safety and Risk Management: Standardization often includes safety requirements and guidelines that mitigate risks associated with product use. For instance, in industries handling hazardous materials or operating heavy machinery, adherence to safety standards minimizes accidents and ensures workplace safety protocols are robust and effective.
Cost Efficiency: Standardization helps streamline manufacturing processes, reduce waste, and optimize resource allocation. By eliminating redundant testing and customization, businesses can achieve economies of scale, lower production costs, and offer competitive pricing without compromising quality.
Global Trade and Market Access: International standards facilitate global trade by harmonizing technical requirements and eliminating trade barriers. Compliance with recognized standards simplifies market access, accelerates product acceptance in new markets, and reduces the need for redundant testing and certification.
Innovation and Continuous Improvement: While standards provide a baseline for quality and safety, they also encourage innovation. Manufacturers and researchers can focus on improving products within established parameters, driving technological advancements and addressing emerging challenges such as environmental sustainability and energy efficiency.
Regulatory Compliance: Many industries are subject to regulatory requirements that mandate adherence to specific standards. Compliance ensures legal conformity and minimizes the risk of fines, penalties, or market exclusions due to non-compliance.
Consumer Protection and Satisfaction: Standardized products are more likely to meet consumer expectations in terms of performance, reliability, and durability. Consumers benefit from consistent quality assurance measures that protect their interests and ensure product reliability over time.
In essence, standardization underpins the efficiency, safety, and competitiveness of industries worldwide. It fosters innovation, facilitates trade, and enhances consumer confidence, making it an essential framework for sustainable economic growth and development.
Major Types of Stainless Steel Pipe Standards
There are several major types of stainless steel pipe standards that govern the specifications, characteristics, and quality requirements of stainless steel pipes used in various industries. Understanding these standards is crucial for ensuring compatibility, performance, and reliability in different applications. Here are the major types:
ASTM Standards for Stainless Steel Pipes
ASTM International, formerly known as the American Society for Testing and Materials, develops and publishes standards for a wide range of materials, including stainless steel pipes. ASTM standards cover aspects such as material composition, mechanical properties, dimensions, testing methods, and quality assurance protocols. These standards are widely recognized and used in industries across the globe.
ASTM A312/A312M: Standard specification for seamless, welded, and heavily cold worked austenitic stainless steel pipes.
ASTM A790/A790M: Specification for seamless and welded ferritic/austenitic stainless steel pipes for general corrosive service.
EN Standards for Stainless Steel Pipes
The European Committee for Standardization (CEN) issues standards known as EN standards, which are widely adopted in Europe and other regions that follow European norms. EN standards cover similar aspects as ASTM standards but may have different designations and technical requirements tailored to European market needs.
EN 10216: Seamless steel tubes for pressure purposes.
EN 10217: Welded steel tubes for pressure purposes.
JIS Standards for Stainless Steel Pipes
The Japanese Industrial Standards (JIS) specify the standards used for industrial activities in Japan. JIS standards for stainless steel pipes ensure compatibility and quality in Japanese industries and are recognized internationally.
JIS G3459: Stainless steel pipes for corrosion resistance, low temperature service, and high temperature service.
JIS G3468: Large diameter welded stainless steel pipes.
DIN Standards for Stainless Steel Pipes
Deutsches Institut für Normung (DIN), or the German Institute for Standardization, develops standards for a wide range of products, including stainless steel pipes. DIN standards are widely used in Germany and throughout Europe, often overlapping with EN standards but with specific German industry requirements.
DIN 17456: General purpose seamless circular stainless steel tubes.
DIN 17457: Welded circular austenitic stainless steel tubes.
ASME Standards for Stainless Steel Pipes
The American Society of Mechanical Engineers (ASME) publishes standards that are widely used in the United States and internationally in industries such as oil and gas, chemical processing, and power generation. ASME standards cover a range of stainless steel pipe applications and are often harmonized with ASTM standards.
ASME B36.19: Stainless steel pipe standardizes dimensions of seamless and welded steel pipe.
ASME B36.10M: Welded and seamless wrought steel pipe.
These major types of stainless steel pipe standards provide comprehensive guidelines for material selection, manufacturing processes, dimensional specifications, testing procedures, and quality assurance protocols. By adhering to these standards, manufacturers, engineers, and end-users ensure that stainless steel pipes meet industry requirements for performance, safety, and reliability across diverse applications and global markets.
Key Parameters Defined by Stainless Steel Pipe Standards
Stainless steel pipe standards define several key parameters that are critical for ensuring the quality, performance, and suitability of stainless steel pipes in various applications. These parameters cover aspects such as material composition, mechanical properties, dimensional requirements, testing methods, and quality assurance criteria. Here’s a detailed look at the key parameters defined by stainless steel pipe standards:
Material Composition Requirements
Stainless steel pipe standards specify the chemical composition of the stainless steel alloys used in pipe manufacturing. The composition typically includes elements such as chromium, nickel, molybdenum, and others, which impart corrosion resistance, strength, and other desired properties.
Chromium (Cr): Enhances corrosion resistance and oxidation resistance.
Nickel (Ni): Improves ductility, toughness, and resistance to corrosion.
Molybdenum (Mo): Enhances resistance to pitting and crevice corrosion, especially in chloride environments.
Carbon (C): Affects strength and hardness of the stainless steel.
Mechanical Properties Specifications
Stainless steel pipe standards define mechanical properties that the material must meet to ensure adequate performance under various operating conditions. These properties include:
Tensile Strength: The maximum stress a material can withstand while being stretched or pulled before breaking.
Yield Strength: The stress at which a material begins to deform plastically (permanently) after being stretched.
Elongation: The amount of deformation a material undergoes before it breaks, expressed as a percentage of its original length.
Dimensional Tolerances and Sizes
Standards specify dimensional requirements for stainless steel pipes to ensure uniformity, compatibility, and ease of installation. This includes:
Outer Diameter: The diameter of the pipe measured across its outer surface.
Wall Thickness: The thickness of the pipe wall.
Length: The specified length of each pipe section.
Tolerances: Allowable deviations from nominal dimensions to accommodate manufacturing variability.
Testing Methods
Stainless steel pipe standards outline specific testing methods to assess the quality and integrity of pipes. Common testing methods include:
Hydrostatic Testing: Testing the strength and leak resistance by subjecting the pipe to water or other fluids under pressure.
Non-Destructive Testing (NDT): Techniques such as ultrasonic testing (UT), radiographic testing (RT), and magnetic particle testing (MT) to detect surface and subsurface defects without damaging the pipe.
Chemical Analysis: Determining the elemental composition of the stainless steel to verify compliance with specified grades.
Quality Assurance Protocols
Standards establish protocols for quality assurance throughout the manufacturing process to ensure consistency and reliability of stainless steel pipes. This includes:
Quality Management Systems: Requirements for implementing and maintaining quality management systems (e.g., ISO 9001) to manage processes and ensure product quality.
Inspection Procedures: Guidelines for inspecting raw materials, in-process manufacturing, and finished products to verify conformity to standards.
Certification: Criteria for certification of compliance with standards, often conducted by independent third-party organizations to provide assurance of product quality.
By defining these key parameters, stainless steel pipe standards ensure that manufacturers produce pipes that meet specified requirements for material composition, mechanical performance, dimensional accuracy, and quality assurance. Adherence to these standards not only ensures product reliability and performance but also facilitates regulatory compliance and enhances confidence among users in diverse industries such as construction, oil and gas, chemical processing, and utilities.
Compliance and Certification Processes
Compliance and certification processes are integral to ensuring that stainless steel pipes meet established standards and regulatory requirements. These processes involve systematic procedures to verify that the pipes manufactured or supplied conform to specified standards for quality, safety, and performance. Here’s an overview of compliance and certification processes related to stainless steel pipes:
Understanding Compliance with Standards
Compliance with stainless steel pipe standards involves adhering to specific guidelines and requirements set forth by standards organizations such as ASTM International, ISO (International Organization for Standardization), ASME (American Society of Mechanical Engineers), and national standards bodies like ANSI (American National Standards Institute) and BSI (British Standards Institution). These standards cover various aspects including material composition, mechanical properties, dimensional tolerances, testing methods, and quality assurance protocols.
Regulatory Requirements: Identifying applicable regulations and legal requirements that govern the production, distribution, and use of stainless steel pipes in different industries and geographic regions.
Standard Specifications: Ensuring that the pipes meet the detailed specifications and criteria outlined in relevant standards, which may include ASTM A312, EN 10216, ASME B36.19, among others.
Certification Bodies and Their Role
Certification bodies play a crucial role in verifying and certifying compliance with standards. These organizations are typically accredited by national or international accreditation bodies to perform independent assessments and issue certificates attesting to compliance. Key aspects include:
Accreditation: Certification bodies must themselves be accredited to ISO/IEC 17065 or equivalent standards, ensuring they operate according to recognized principles of impartiality, competence, and consistency.
Audits and Assessments: Conducting audits and assessments of manufacturing processes, quality management systems, and product samples to verify conformity with applicable standards.
Issuance of Certificates: Providing certificates or declarations of conformity that document compliance with specific standards and regulatory requirements.
Quality Management Systems (QMS)
Implementing effective QMS is essential for maintaining compliance with standards throughout the manufacturing process. Key elements include:
Documented Procedures: Establishing documented procedures and work instructions that align with standard requirements and ensure consistency in manufacturing operations.
Process Control: Monitoring and controlling critical processes to ensure product quality and compliance with dimensional tolerances, material specifications, and performance requirements.
Continuous Improvement: Emphasizing continuous improvement through corrective and preventive actions, internal audits, and management reviews to enhance product quality and compliance over time.
Testing and Validation
Testing and validation are integral parts of the certification process to ensure that stainless steel pipes meet performance and safety requirements. Common tests include:
Mechanical Testing: Testing for tensile strength, yield strength, elongation, and hardness to verify mechanical properties.
Non-Destructive Testing (NDT): Using methods like ultrasonic testing (UT), radiographic testing (RT), and dye penetrant testing (PT) to detect defects without damaging the pipe.
Chemical Analysis: Analyzing the chemical composition of materials to ensure they meet specified standards and grades.
Compliance Documentation and Traceability
Maintaining comprehensive documentation and traceability throughout the supply chain is crucial for demonstrating compliance and ensuring product integrity. This includes:
Material Traceability: Tracking the origin and history of materials used in manufacturing to verify compliance with specified standards and specifications.
Certificates of Conformity: Providing documentation such as test reports, inspection records, and certificates of conformity to demonstrate compliance with standards and regulatory requirements.
Product Marking and Labeling: Marking products with relevant information such as material grade, standard designation, and manufacturer’s identification to facilitate traceability and compliance verification.
Compliance and certification processes for stainless steel pipes ensure that products meet stringent quality, safety, and performance standards required by industries and regulatory authorities. By adhering to these processes, manufacturers and suppliers not only enhance product reliability and market acceptance but also contribute to overall industry safety and sustainability efforts. Effective implementation of compliance and certification practices promotes trust and confidence among stakeholders and supports global trade by ensuring consistency and reliability of stainless steel pipe products.