Summary:
Revealing the Secrets of Stainless Steel Welding: Skills, Methods, and Practical Guidelines
Choose the appropriate stainless steel welding method
The Art of Balancing Current and Voltage
Selection and treatment of welding materials
Stainless steel welding is an important field in welding technology, and its particularity requires welders not only to have a solid technical foundation, but also to master different welding methods and practical application skills. This article will delve into the core techniques and best practices of stainless steel welding, aiming to help professional welders and enthusiasts better understand the key points of stainless steel welding and improve welding quality.
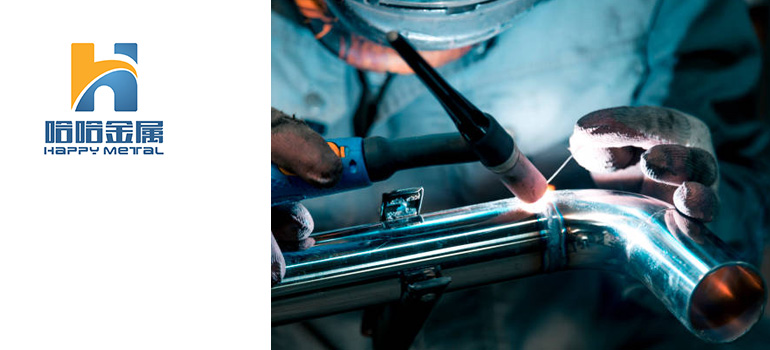
Choose the appropriate stainless steel welding method
Proficient in TIG welding technology
TIG (argon arc welding) is widely used in projects that require high quality and precision welding. TIG welding provides higher welding control and less slag generation, making it suitable for stainless steel sheets and occasions with high aesthetic requirements. In practice, welders need to master the steps, skills, and scope of application of TIG welding to ensure the stability of the welding process and the quality of the weld seam.
Master the key points of MIG welding
MIG (Gas Metal Arc Welding) is an efficient and fast stainless steel welding method, especially suitable for large-scale engineering. MIG welding can complete a large amount of welding work in a short period of time, but in practice, attention should be paid to the management of slag and the adjustment of welding parameters. This section will delve into the advantages, applicability, and key techniques of MIG welding, helping welders better cope with challenges in complex work environments.
The Art of Balancing Current and Voltage
Deep analysis of the impact of current
Current is one of the key factors affecting the formation of welding pools and the quality of welds. Different stainless steel materials require different current settings, so welders need to understand the impact of current on welding. Adjusting the current can change the width and depth of the weld seam, while also affecting the stability of the melt pool. This section will delve into the techniques of current adjustment and the methods to achieve optimal welding results under different working conditions.
Tips for voltage setting
Like current, an appropriate voltage setting is crucial for stainless steel welding. The adjustment of voltage affects the length of the welding arc and the speed of droplet transfer. In practice, welders need to adjust the voltage according to specific welding tasks to achieve the best welding effect. This section will provide practical voltage adjustment suggestions to help welders better grasp the welding process in different situations.
Selection and treatment of welding materials
The Mystery of Welding Wire
Choosing the appropriate welding wire is crucial for stainless steel welding. Different types of stainless steel require the use of specific welding wires, for example, for 304 stainless steel, the commonly used welding wire is the 308 series. Understanding the characteristics of different welding wires and selecting welding wires suitable for specific projects is the key to ensuring the quality of welding joints. This section will provide a detailed introduction to the characteristics of different types of welding wires and their selection principles in practice.
Selection and Techniques of Solder Flux
Flux plays an important role in stainless steel welding. Choosing a flux suitable for stainless steel can help reduce the generation of pores and improve welding quality. Stainless steel has high oxidation resistance, so special attention should be paid to compatibility with stainless steel when selecting flux. This section will explore the characteristics of different types of fluxes and the techniques for using fluxes in actual welding.
By conducting in-depth research on the key techniques of stainless steel welding, selecting appropriate welding methods, balancing current and voltage, and correctly handling welding materials, welders will be able to stand out in stainless steel welding projects. These practical suggestions are not only applicable to professional welders, but also provide valuable guidance for welding enthusiasts. In the increasingly competitive welding field, constantly learning and improving one’s skills will be the key to success. Through the knowledge provided in this article, we believe that readers can more confidently cope with various stainless steel welding challenges and achieve better welding results.